¿Experimentos, big data o gráficos de control de Shewhart?
Artículo de Donald Wheeler: "Diferentes enfoques para la mejora de procesos. ¿Su enfoque hace lo que usted desea?"
DONALD J. WHEELER: "Diferentes enfoques para la mejora de procesos. ¿Su enfoque hace lo que necesita?"
Traducción: Director Científico del Centro AQT
Serguéi P. Grigoriev
.
El libre acceso a los artículos no disminuye en modo alguno el valor de los materiales contenidos en ellos.
Hoy en día, se proponen varios enfoques para la mejora de procesos. Evaluar cómo funciona cada enfoque es fundamental para elegir cuál será eficaz. Aquí analizamos el problema de la producción y cómo diferentes enfoques de mejora resuelven este problema.
problema de producción
Para los propósitos de la siguiente discusión, existirá una relación causal cuando cambios en el significado de la causa resulten en cambios en el significado de la característica del producto. Aquí definimos causa efecto como la variación creada en el flujo de un producto cuando la causa cambia en su rango natural de valores. Cuando la causa es limitada y no puede cambiar, ya no creará ningún cambio en el flujo de valor del producto.
Cualquier característica específica de un producto fabricado será el resultado de docenas, si no cientos, de relaciones causa-efecto. Estas causas se pueden dividir en dos grupos: aquellas causas que sabemos lo suficientemente bien como para nombrarlas y aquellas causas que actúan sin nuestro conocimiento y, por lo tanto, permanecen desconocidas para nosotros. Antes de comenzar la producción, es posible que se desconozcan las consecuencias de todas estas causas, lo que da como resultado una imagen similar a la Figura 1.
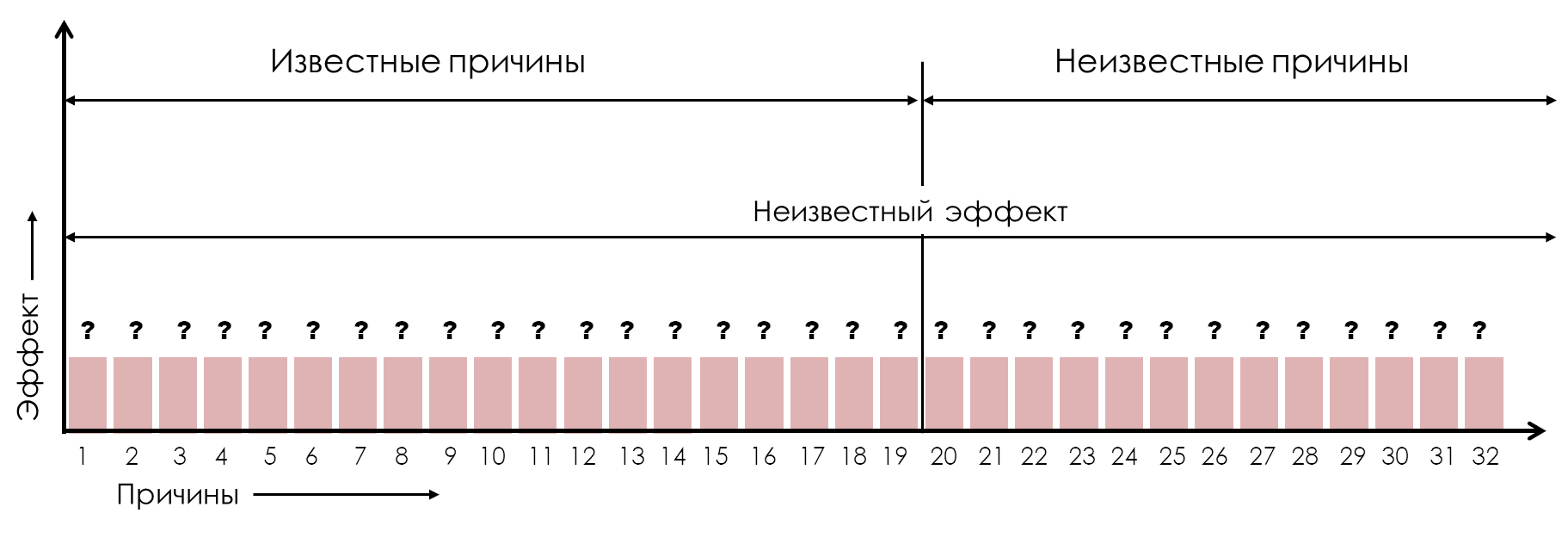
Figura 1: Dos categorías de relaciones causa-efecto
Normalmente, la I+D estudia un subconjunto de causas conocidas para determinar sus consecuencias. Estos motivos estudiados serán aquellos que se considere que tienen una influencia pronunciada en las características del producto. Una vez que se conocen estos efectos, este conjunto de causas aprendidas se puede organizar en un diagrama de Pareto (Grupos I, II) como se muestra en la Figura 2.
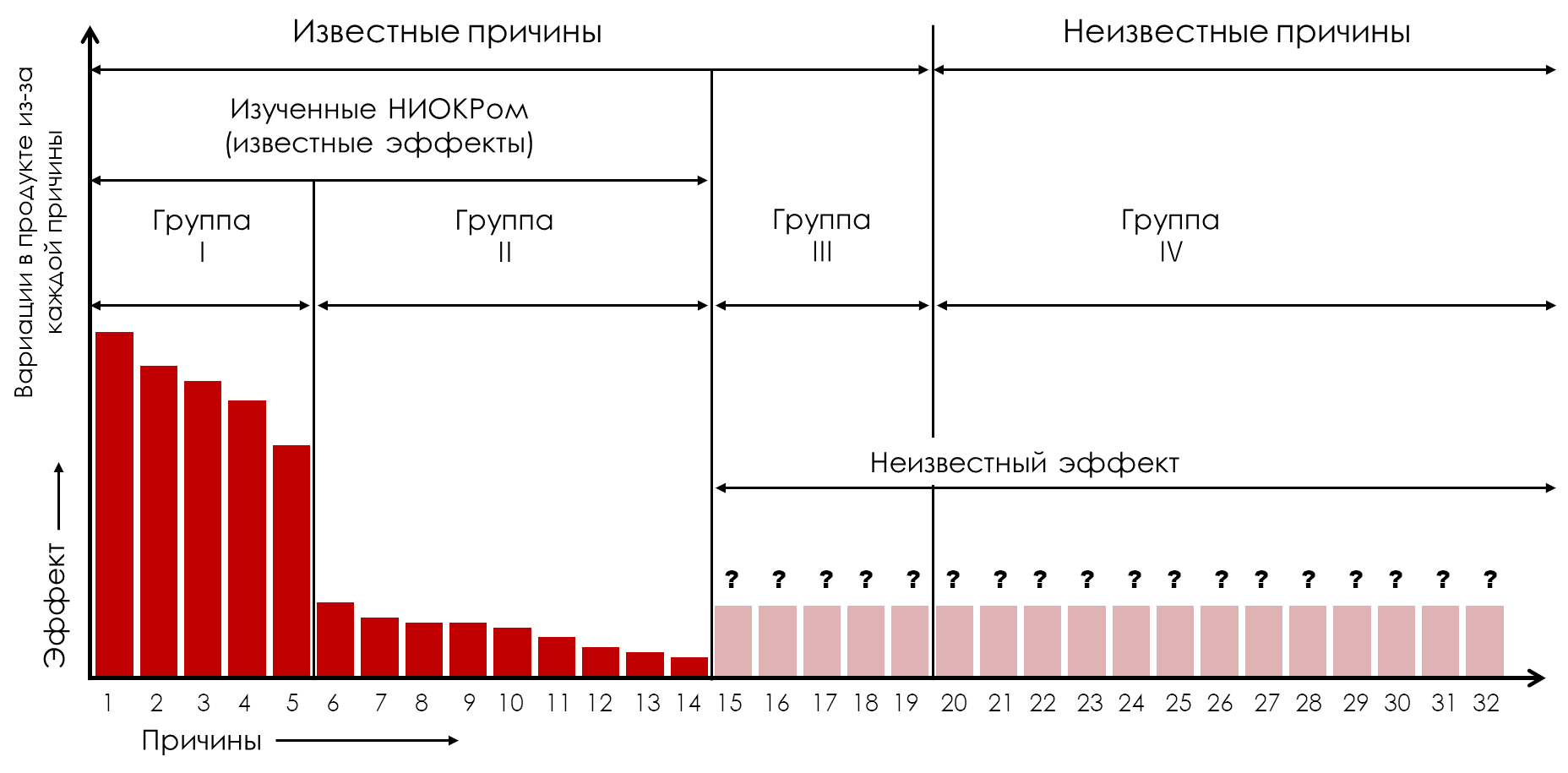
Figura 2: Diagrama de Pareto de efectos conocidos para las causas estudiadas (Grupos I, II)
Designemos las razones del primero al quinto como razones del primer grupo (Figura 2, Grupo I). Estas causas tienen efectos dominantes y son las causas que queremos controlar durante la producción. Al mantener constantes estas cinco causas, eliminaremos eficazmente su influencia del flujo del producto. Al mismo tiempo, los valores fijos elegidos para cada una de estas cinco causas determinarán colectivamente el valor medio del proceso.
Las razones del 6 al 14 son razones del segundo grupo (Figura 2, Grupo II). Estas causas tienen consecuencias tan menores que no intentaremos controlarlas en producción. (Estas suelen ser las razones por las que los costos del control exceden los beneficios del control).
Entre las 14 causas de I+D examinadas, si no se hiciera ningún intento por controlarlas, los efectos de cinco causas en el grupo uno representarían el 85 por ciento de la variación en el flujo de productos, mientras que las nueve causas restantes en el grupo dos contribuirían con el 15 por ciento de la variación en el flujo de productos. La variación. Así, controlando el primer grupo de causas, eliminamos el 85 por ciento de la variación en el flujo de producto provocada por las causas estudiadas.
Las causas del tercer grupo (Figura 2, Grupo III) son aquellas causas conocidas que no han sido estudiadas por I+D. Normalmente se trata de causas cuyas consecuencias se consideraron mínimas y, por tanto, no dignas de estudio. Sin embargo, como se muestra en la Figura 2, estas causas en realidad tendrán consecuencias desconocidas.
Por conveniencia, denotamos la totalidad de todas las relaciones de causa y efecto desconocidas que afectan nuestro proceso sin nuestro conocimiento como causas del cuarto grupo (Grupo IV).
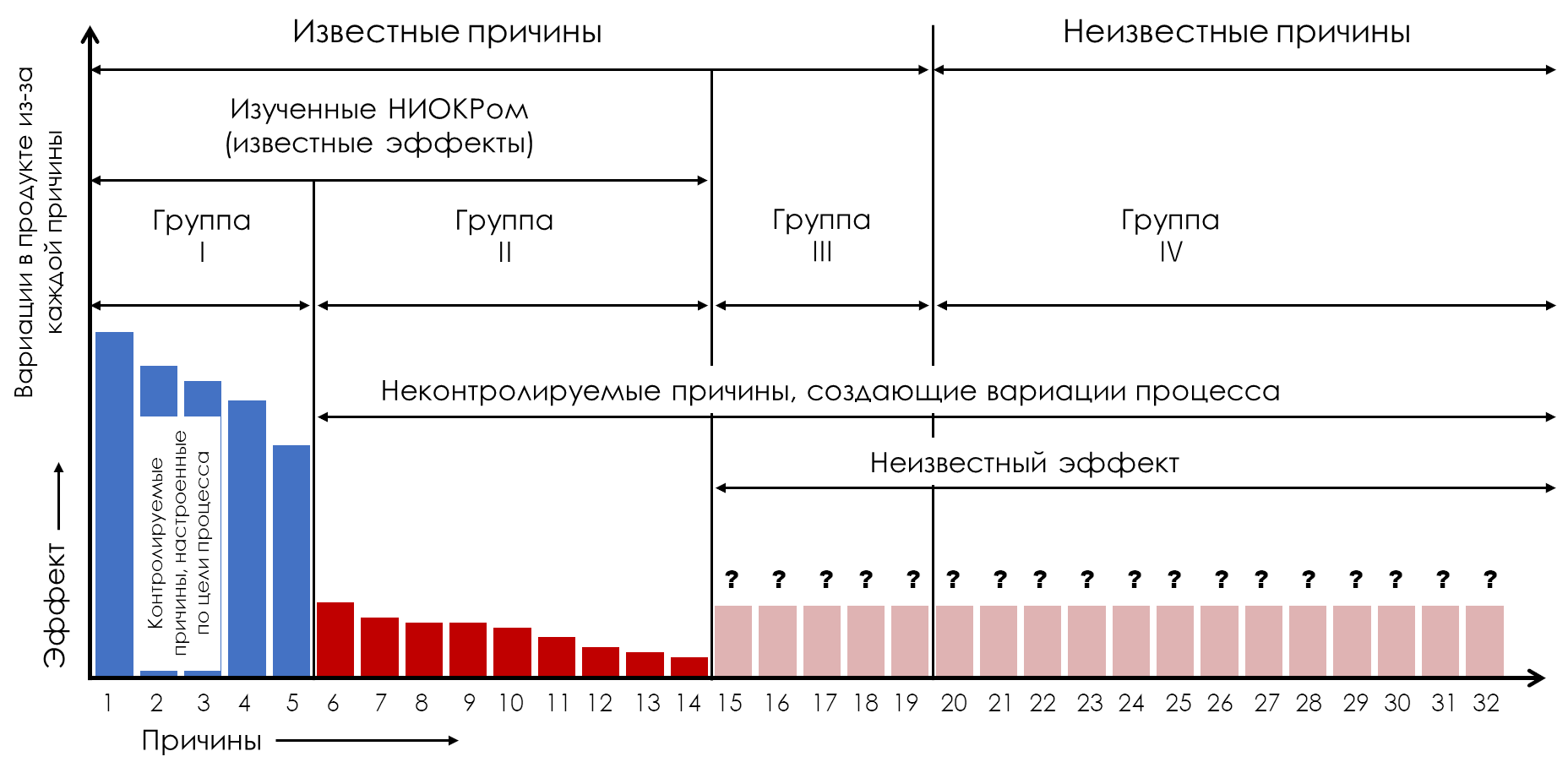
Figura 3: La variación del proceso se produce debido a todas las causas incontrolables.
Desafortunadamente, las variaciones en el flujo de productos producidos no se limitan a las causas del segundo grupo (Grupo II). Las causas del tercer (Grupo III) y del cuarto (Grupo IV) también contribuyen a esta variación. Dado que las causas en estos tres grupos (Grupos II, III, IV) son diferentes, cada una contribuirá a la variación en las características del producto, y todas estas fuentes de variación se sumarán a la variación en el flujo del producto. Es por ello que las variaciones observadas en la producción suelen superar las variaciones previstas por la I+D.
Finalmente, no hay garantía de que todos los efectos desconocidos de las causas de los Grupos III y IV sean insignificantes. Además, estos efectos pueden cambiar con el tiempo. Estos cambios pueden ocurrir debido al desgaste, cambios de personal, desarrollos en los métodos de trabajo y cambios en el suministro de materiales. Cuando se producen estos cambios, pueden dificultar aún más la mejora de los procesos.
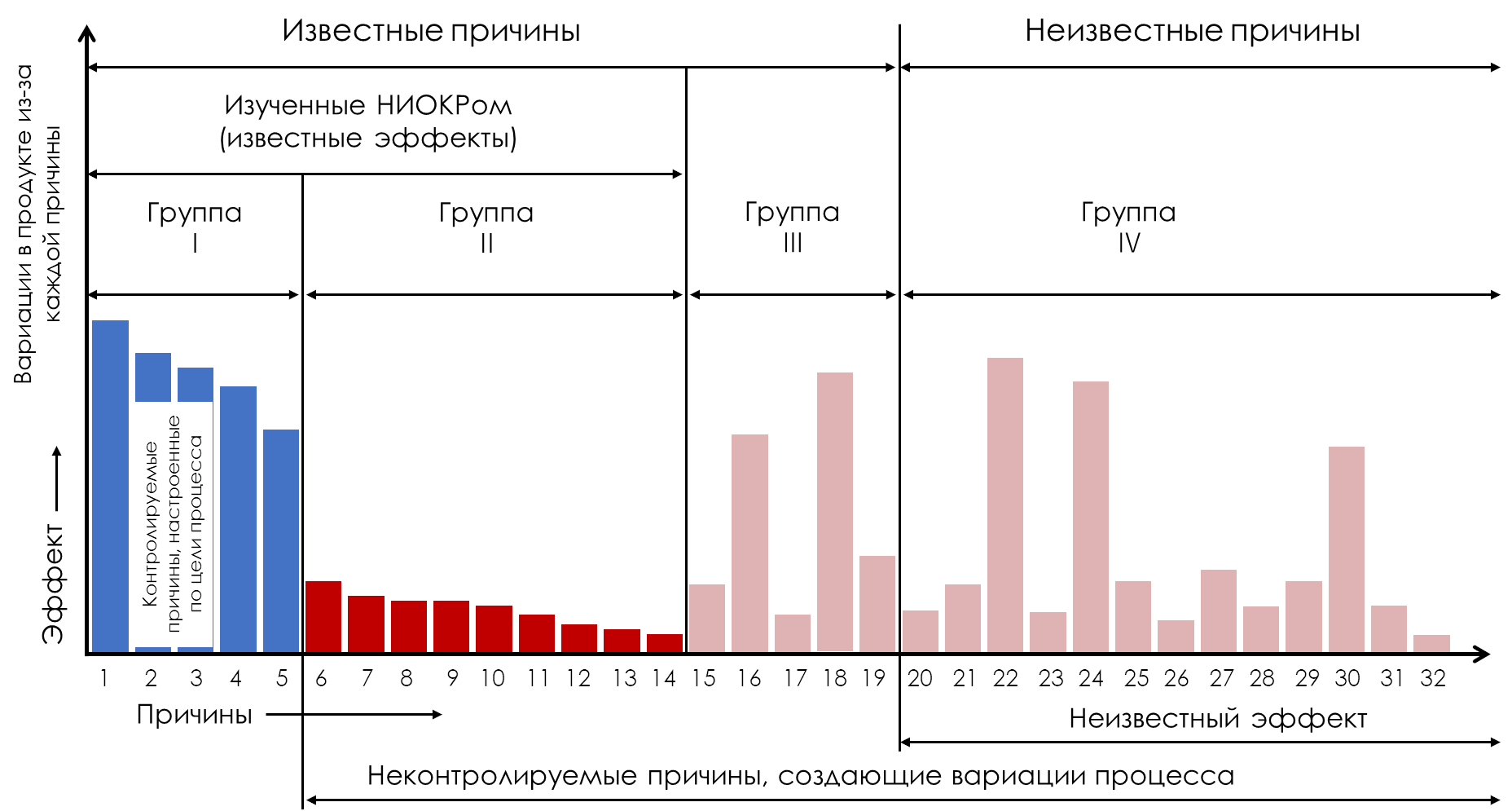
Figura 4: Algunas causas incontrolables pueden tener efectos dominantes.
Por lo tanto, las figuras 3 y 4 proporcionan un marco contra el cual podemos evaluar diferentes enfoques de mejora. Caracterizan lo que sabemos y lo que no sabemos para que podamos ver cómo se relaciona un enfoque particular con cada elemento del problema de mejora de procesos.
En la Figura 3 vemos que los problemas de ajustar un proceso a su objetivo (nominal) estarán asociados con la elección de niveles para las causas en el primer grupo (Grupo I). Los problemas de reducción de la variación en el flujo de productos estarán asociados con causas de los otros tres grupos (Grupos II, III, IV).
Entonces, ¿cómo podemos reducir la variabilidad del proceso? Esencialmente, la única manera de reducir la variación es eliminar el efecto del flujo de productos manteniendo su causa en algún nivel fijo. En otras palabras, eliminamos la variación moviendo una causa del segundo, tercer o cuarto grupo (Grupos II, III, IV) al primer grupo (Grupo I).
Sin embargo, antes de que trasladar una causa al primer grupo (Grupo I) sea rentable, los beneficios deben superar los costos. Esto significa que la causa debe tener un efecto dominante antes de que sea económicamente viable intentar controlarla.
Así, la tarea de reducir la variabilidad del proceso es encontrar causas con efectos predominantes en el segundo, tercer o cuarto grupo (Grupos II, III, IV), y luego transferir estas causas al primer grupo (Grupo I).
Enfoques experimentales
Varios enfoques para la mejora de procesos se basan en una serie de experimentos. Los experimentos nos permiten estudiar causas individuales para cuantificar su impacto en una característica determinada del producto. Estos enfoques experimentales cubren todo, desde experimentos simples de una sola causa hasta experimentos diseñados con múltiples causas. Independientemente de la complejidad, los estudios experimentales siempre requieren la manipulación de las entradas del proceso. Esto limita los enfoques experimentales para estudiar causas conocidas del primer, segundo o tercer grupo (Grupos I, II, III).
Una vez estudiados los motivos del primer grupo (Grupo I), se realizará un estudio de optimización. Aquí se esforzará por encontrar una combinación de valores de las razones del primer grupo que conduzca al valor óptimo para hacer coincidir la característica del producto estudiado con el objetivo del proceso (nominal).
Cuando se utilizan estudios experimentales con causas de los grupos dos o tres (Grupos II, III), el objetivo es identificar cualquier causa que pueda tener un efecto dominante. Cuando se identifican dichas causas, se pueden trasladar al primer grupo para eliminar sus variaciones del flujo del producto. Por supuesto, los experimentos con causas del Grupo 2 (Grupo II) buscarán efectos grandes donde la I+D originalmente encontró sólo efectos pequeños. Y los experimentos que investiguen las causas del Grupo 3 (Grupo III) buscarán efectos grandes donde se pensaba que no existían. Sin embargo, con el tiempo, debido al desgaste y otros efectos de la entropía, causas que antes tenían poco efecto pueden convertirse en causas de gran efecto.
Por esta razón, a veces pueden resultar útiles experimentos con causas del segundo y tercer grupo (Grupos II, III). En la Figura 4, se encontró que las razones 16 y 18 (Grupo III) tenían efectos dominantes y, por lo tanto, se trasladaron del Grupo 3 al Grupo 1 (Figura 5). Esto redujo el costo promedio de producción y uso (ACP&U) para este proceso al 75 por ciento de lo que era en la Figura 4.
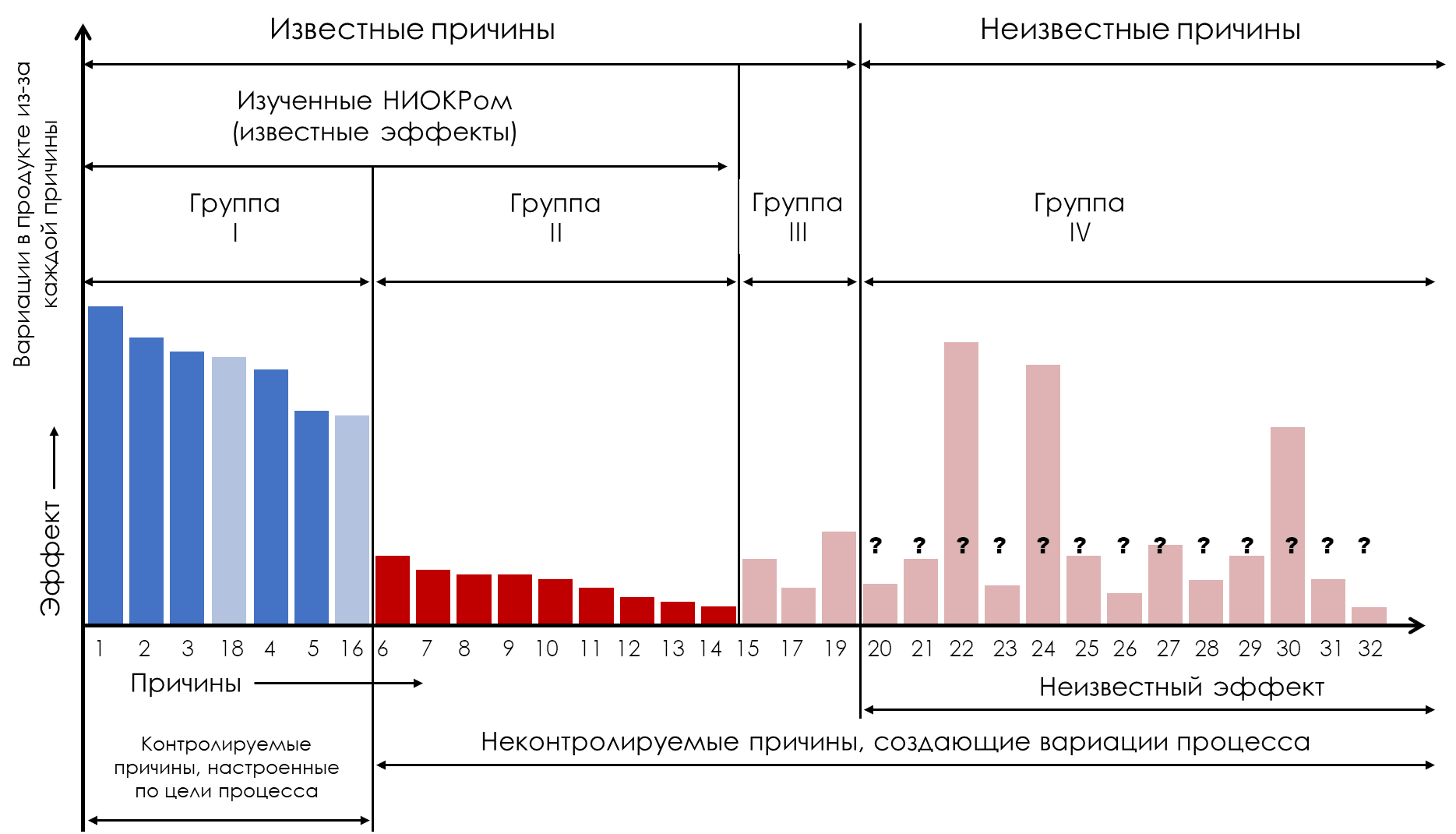
Figura 5: Qué resultados experimentales se pueden lograr
Pero ¿qué pasa con las causas del cuarto grupo (Grupo IV)? Aunque no podemos estudiar causas desconocidas en un experimento, esto no significa que nuestros resultados experimentales estén libres de la influencia de causas desconocidas en el cuarto grupo. Si la causa dominante del cuarto grupo cambia durante el experimento, puede arruinar el análisis y arruinar el experimento. (La mayoría de los estadísticos pueden contarle historias sobre lo que sucedió cuando alguna variable extraña ajena al estudio interfirió con el experimento).
Por lo tanto, aunque los estudios experimentales son esenciales para el diseño de procesos y nos permiten analizar los efectos de diferentes entradas del proceso, enfrentan ciertas limitaciones en las tareas de mejora de procesos. Aunque los experimentos nos permiten obtener respuestas concretas a preguntas concretas, su utilidad es limitada cuando no sabemos qué preguntas hacer.
Enfoques observacionales
La investigación experimental siempre comienza con la identificación de un conjunto de causas a estudiar. Los enfoques observacionales no hacen esto. Más bien, buscan obtener información sobre un proceso utilizando datos existentes. Como los datos existentes normalmente se obtendrán mientras las causas del grupo 1 (Grupo I) permanecen constantes, los enfoques observacionales tenderán a centrarse en causas incontrolables.
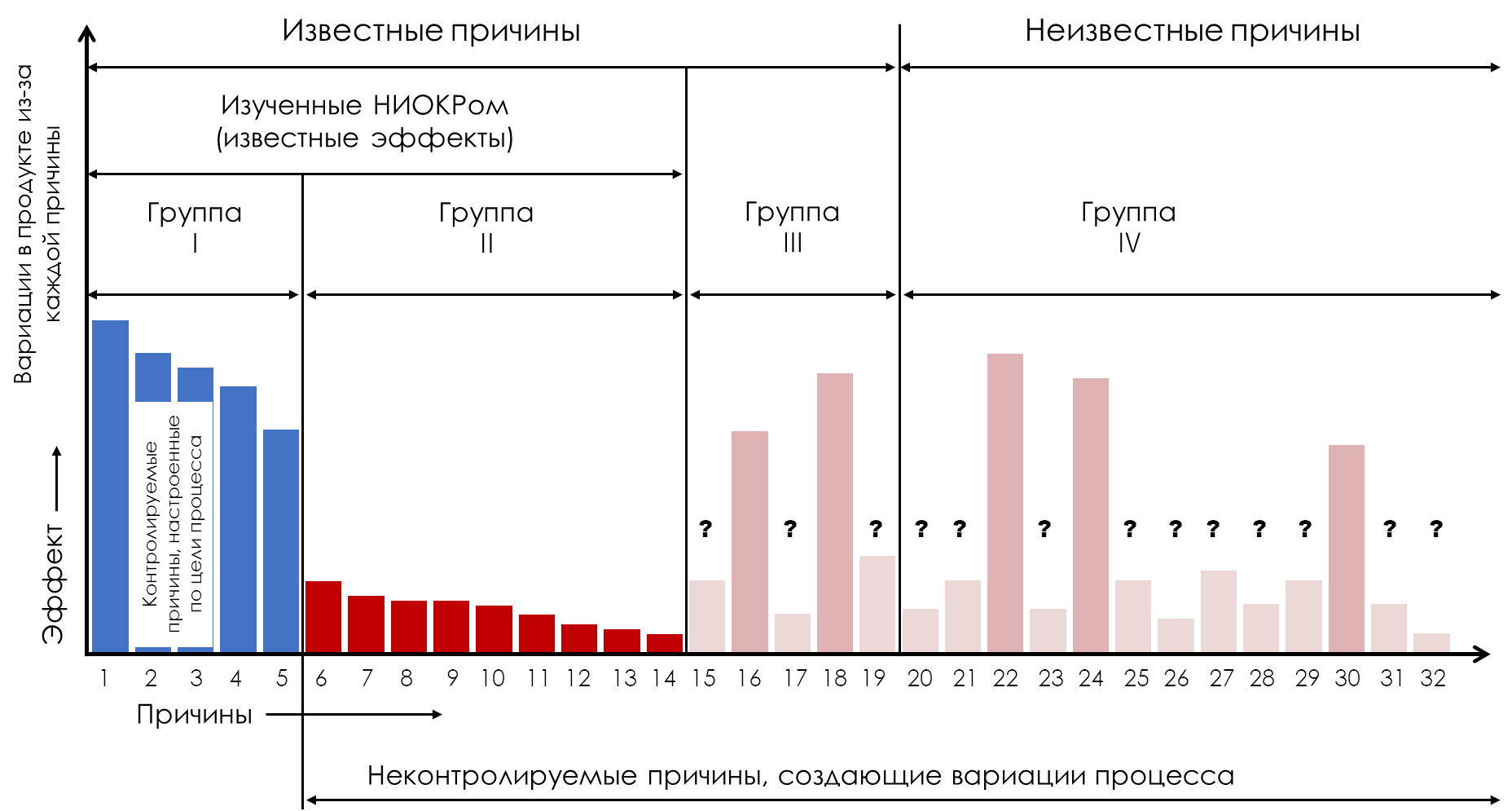
Figura 6: Lo que necesitamos saber
La idea detrás del enfoque observacional es que realmente no necesitamos conocer los tamaños de todos los efectos en la Fig. 6. Más bien, solo necesitamos saber qué causas incontrolables tienen los efectos dominantes (aquí las causas 16, 18, 22, 24 y 30). Una vez que sabemos qué causas tienen efectos lo suficientemente grandes como para cambiar el flujo de productos, sabemos qué causas deben trasladarse al primer grupo (Grupo I). Y podemos tomar esta decisión sobre estas causas sin cuantificar realmente el tamaño de sus consecuencias. A continuación se explicarán las características de los dos tipos principales de estudios observacionales.
Enfoques para el seguimiento de datos
Gracias a la potencia informática actual, se están volviendo populares nuevos e ingeniosos enfoques para analizar los datos existentes. Estos enfoques solían denominarse seguimiento de datos, pero hoy se conocen como enfoques de big data, inteligencia artificial o aprendizaje automático. Independientemente del nombre, estos enfoques recopilan todos los datos disponibles en una base de datos y utilizan algunas técnicas matemáticas para encontrar patrones, agrupaciones o relaciones en los datos. Por muy prometedor que parezca, y sin importar cuántas variables se utilicen, el principal problema de estos enfoques es que los datos siempre tendrán un contexto incompleto.
El contexto es tan importante para el análisis que es el primer axioma del análisis de datos: ningún dato tiene significado fuera de contexto. Sin embargo, los enfoques de seguimiento de datos nunca tendrán un contexto completo. No importa cuántas variables incluyas en la base de datos, nunca podrás incluir variables del cuarto grupo (Grupo IV). Las relaciones de causa y efecto desconocidas nunca se medirán y, por lo tanto, no pueden formar parte de la base de datos. (Si supiéramos lo suficiente para medir sus efectos, serían causas conocidas en lugar de causas desconocidas). Por lo tanto, si bien los enfoques de seguimiento de datos pueden ayudarle a descubrir relaciones entre las causas conocidas y las características de su producto, no pueden identificar ninguna razón desconocida.
El supuesto implícito detrás de todos los métodos de seguimiento de datos es que existe una homogeneidad de condiciones detrás de los datos: que las variables no incluidas en la base de datos no tienen un efecto real sobre los resultados que se estudian. Sin embargo, no existe una prueba efectiva de este supuesto fundamental. Cuando causas desconocidas dominan un proceso, pueden distorsionar completamente los patrones detectados por los métodos de seguimiento de datos. Por lo tanto, aunque estos enfoques intentan encontrar patrones entre variables conocidas, pueden verse socavados por variables del cuarto grupo (Grupo IV).
Listas de verificación del comportamiento del proceso
Los gráficos de control del comportamiento de los procesos (gráficos de control de Shewhart) han demostrado ser un enfoque observacional para la mejora de procesos. Ellos dan definición operacional cómo sacarle el máximo partido a cualquier proceso. Los registros actuales de desempeño del producto (puntos en el gráfico de control) reflejan el desempeño real del proceso. Los límites del gráfico de control definen el potencial del proceso: lo que el proceso es capaz de lograr cuando opera según lo previsto con una variación mínima. Al mapear el desempeño del proceso con el potencial del proceso, un gráfico de control del comportamiento del proceso le permite evaluar qué tan cerca está un proceso de operar a su máximo potencial. También nos permite determinar cuándo ha ocurrido un cambio en el proceso. Y estos cambios son la clave para identificar causas desconocidas con efectos dominantes del cuarto grupo (Grupo IV).
Algunos críticos que no entienden cómo funcionan los gráficos de control de Shewhart afirman que están "obsoletos". Pero cuando se trata de matemáticas, la edad no devalúa la técnica ni cambia su aplicabilidad. El teorema de Pitágoras tiene al menos 2500 años. Walter Shewhart creó el diagrama de control del comportamiento del proceso hace más de 90 años. El concepto detrás del gráfico de control es 2200 años más antiguo. Fue Aristóteles quien nos enseñó que debemos fijarnos en aquellos puntos donde un sistema cambia para poder descubrir las causas que afectan al sistema. Y esto es esencialmente lo que nos permiten hacer los gráficos de control del comportamiento del proceso.
Al identificar los puntos en los que cambia un proceso, un gráfico de control del comportamiento del proceso nos permite detectar causas con efectos dominantes originados en cualquiera de los cuatro grupos (Grupos I, II, III, IV).
Al esperar a que el proceso demuestre un cambio de comportamiento, también permitimos que el proceso priorice las causas según el tamaño de sus efectos. De esta manera descubrimos aquellas causas que tienen efectos dominantes, sin perder tiempo y esfuerzo en estudiar muchas causas con efectos insignificantes.
Sólo con el enfoque de Shewhart y Aristóteles podemos descubrir las causas desconocidas del cuarto grupo (Grupo IV) que tienen efectos dominantes. Aunque un gráfico de control del comportamiento del proceso puede identificar causas conocidas y desconocidas con efectos dominantes que crean las señales detectadas por los gráficos de control del comportamiento del proceso, la capacidad de aprender sobre las causas del cuarto grupo (Grupo IV) es el principal beneficio del uso de gráficos de control. . Esto nos permite aprender sobre errores, malas prácticas y cosas estúpidas que realmente suceden en la fabricación pero que nunca se estudiarían en ningún programa de investigación y desarrollo (I+D). Y esto nos permite detectar en tiempo real cuando algo va mal para poder corregirlo a tiempo. Por tanto, los gráficos de control del comportamiento del proceso son más generales y confiables que otros enfoques.
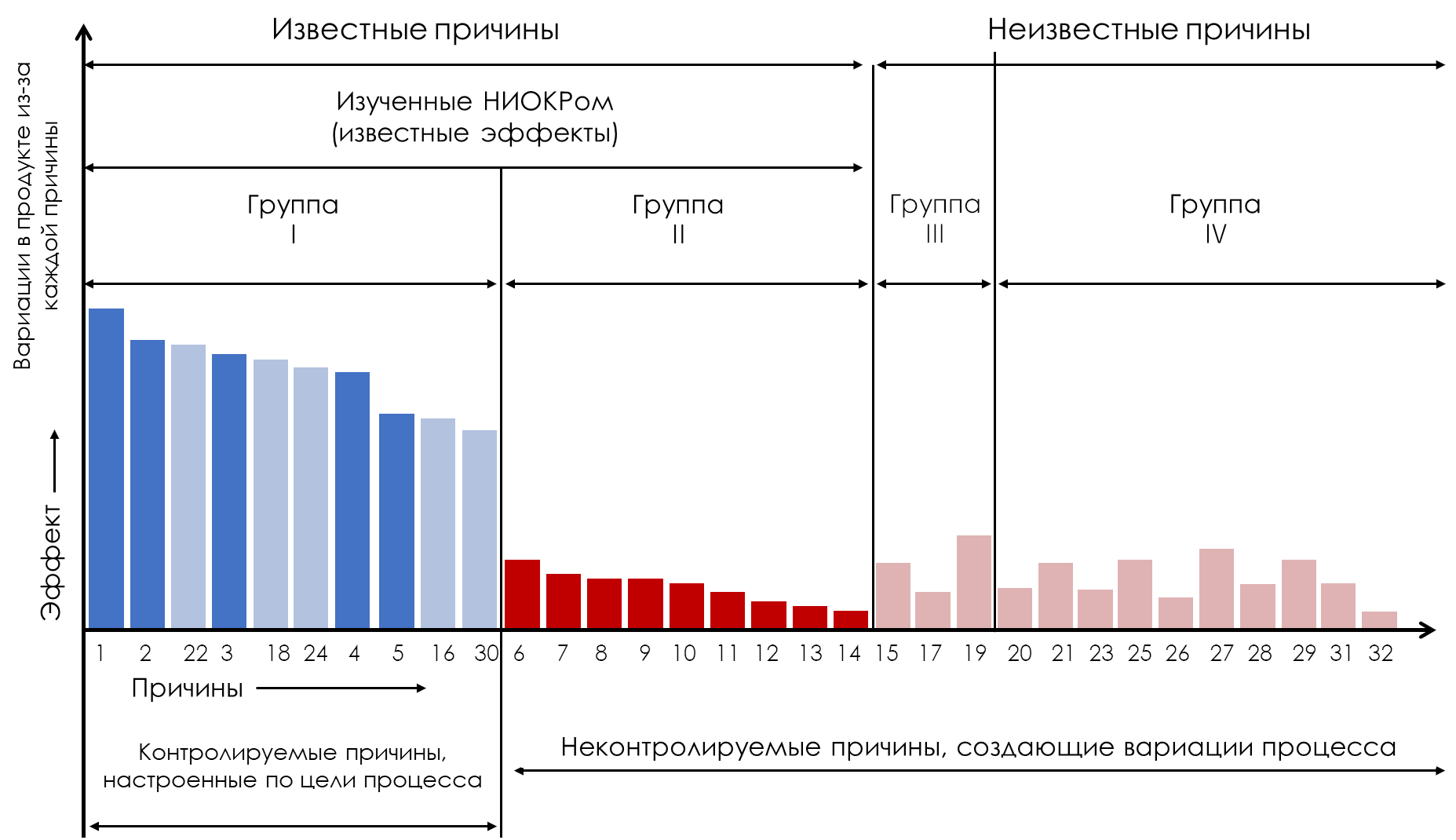
Figura 7. Qué se puede lograr con un gráfico de control del comportamiento del proceso
Para el proceso que se muestra en la Fig. 7, el costo promedio de producción y uso (ACP&U) será solo el 25 por ciento del costo promedio de producción y uso para el proceso que se muestra en la Fig. 4. El aumento cuatro veces mayor en calidad y productividad se debe al movimiento de las razones: 22, 18, 24, 16 y 30 en el primer grupo.
Ver explicación de este párrafo en la descripción. Funciones de pérdida de calidad de Taguchi .
Resumen
Los enfoques experimentales para la mejora de procesos sólo pueden estudiar las relaciones causa-efecto conocidas. Aunque estos estudios son necesarios para el ajuste de procesos, tienen limitaciones como método de mejora de procesos. Los estudios de causa en el primer y segundo grupo (Grupos I, II) replicarán estudios anteriores, y los estudios de causa en el tercer grupo (Grupos III) tendrán como objetivo encontrar pepitas que se perdieron en estudios anteriores. Por lo tanto, los estudios experimentales de las causas en los grupos segundo y tercero (Grupos II, III) requerirán tiempo, dinero y esfuerzo para confirmar esencialmente que la mayoría de estas causas todavía tienen efectos insignificantes. Además, los experimentos no pueden estudiar las causas del cuarto grupo (Grupo IV), y los resultados experimentales pueden verse socavados por el hecho de que las causas del cuarto grupo tengan un efecto dominante.
Los enfoques para rastrear datos para mejorar procesos incluyen big data, inteligencia artificial y técnicas de aprendizaje automático que buscan modelar datos y descubrir relaciones utilizando causas en el segundo y tercer grupo (Grupos II, III). Desafortunadamente, a pesar de su complejidad y sofisticación, estos enfoques también pueden verse socavados por el cuarto grupo de causas (Grupo IV) con efectos dominantes.
Sólo un gráfico de control del comportamiento del proceso busca explícitamente fallas causadas por causas conocidas y desconocidas. El enfoque de Aristóteles para estudiar los puntos en los que cambia un proceso nos permite descubrir cosas que están más allá del alcance de los estudios experimentales y que no pueden detectarse mediante métodos de seguimiento de datos. Además, el enfoque del gráfico de control del comportamiento del proceso no pierde tiempo ni esfuerzo en cuantificar efectos triviales. Al centrarse siempre en causas con efectos dominantes, los gráficos de control del comportamiento de los procesos nos permiten aprender a ejecutar nuestros procesos de forma predecible, con una variación mínima y con precisión en el objetivo.
Entonces, si está seguro de que puede descubrir algo que los investigadores y desarrolladores han pasado por alto, entonces siga adelante y adopte un enfoque experimental para mejorar los procesos.
O, si, a diferencia de Aristóteles, está seguro de que su proceso no cambia con el tiempo, utilice uno de los enfoques de seguimiento de datos para mejorar el proceso. La complejidad y sofisticación de estas técnicas no dejarán indiferente a nadie. Pero tenga en cuenta que sus resultados pueden ser tan confiables como un castillo de naipes.
Si simplemente desea mejorar su proceso, utilice las Listas de verificación de comportamiento del proceso para aprender cómo utilizar su proceso en todo su potencial. Nada se acerca siquiera a dar tanto con tan poco esfuerzo.