El plan de todo o nada está en contra del uso de tablas para la inspección aleatoria de aceptación de calidad. Edwards Deming
"El uso de tablas de inspección por muestreo de aceptación no se puede adaptar para minimizar el costo total promedio de la inspección de materiales entrantes y las consecuencias de permitir la entrada de materiales defectuosos en producción".
Fuente de los materiales citados: [2] - W. Edwards Deming, “Out of the Crisis” (“Fuera de la crisis”, W. Edwards Deming - M.: Alpina Publisher, 2017. Editores científicos Y. Rubanik, Y. Adler , V. Shper). Puedes adquirir el libro en la editorial. Editorial Alpina .
El artículo fue elaborado por el director científico del Centro AQT. Serguéi P. Grigoriev
El libre acceso a los artículos no disminuye en modo alguno el valor de los materiales contenidos en ellos.
Prefacio
¿Deberíamos intentar rechazar algunos o todos los artículos defectuosos en un envío entrante? ¿O deberíamos enviar cada lote, sin pasar la inspección, directamente a producción? Una solución económicamente sólida sería utilizar el plan de control de “todo o nada” para las materias primas, materiales y componentes entrantes propuesto por Edwards Deming.
En cualquier caso, ni un solo producto fabricado por la empresa que no cumpla los requisitos debería llegar a nuestro comprador.
La regla de control de insumos de todo o nada se utiliza para minimizar el costo total promedio por unidad de producción de una empresa. La regla "todo o nada" es una regla para tomar una decisión sobre el control del 100% de un lote entrante de materiales con el rechazo de los defectuosos o la liberación de dicho lote a producción sin control entrante, seguido de la sustitución y reelaboración de la proporción de productos defectuosos formados como resultado de dicho pase sin control de entrada.
Si realiza una inspección de entrada de materias primas, materiales y componentes para el control de muestreo, es mejor saber que:
“Si el grado de control estadístico sobre la calidad de los materiales entrantes es alto, el control de las muestras no proporcionaría información sobre el resto del lote inspeccionado, debido a la falta de evidencia de correlación entre ellos en este caso”.
Una confirmación práctica de la afirmación de Edwards Deming de que el control por muestreo, por ejemplo, utilizando tablas de control de calidad de aceptación aleatoria, no da una idea del número de productos defectuosos en el lote controlado, puede ser experimentar con cuentas rojas , en el que muestras mecánicas aleatorias de una mezcla de perlas rojas y blancas dan cada vez un valor de la proporción de perlas rojas que difiere de la proporción real de perlas rojas en la mezcla controlada, tanto mayor como menor. El experimento utilizó un gráfico np de control del número de cuentas rojas para muestras del mismo tamaño.
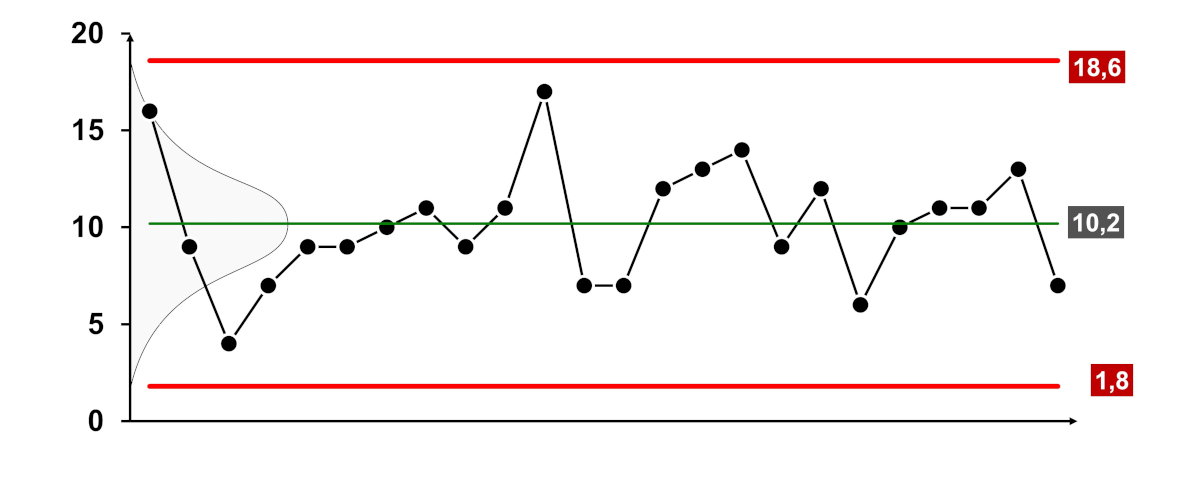
Arroz. Gráfico np de control del experimento de cuentas rojas realizado por Edwards Deming en 1983.
“Las reglas para minimizar los costes medios totales resultan extremadamente sencillas en algunas condiciones.
Designaciones:
p es la proporción promedio de productos defectuosos en el lote de piezas entrante;
k 1 - coste de la inspección entrante de una pieza;
k 2 - el costo de desmantelar, reparar, reensamblar y volver a probar una unidad que falló debido a una pieza defectuosa que entró en producción.
Condición 1:
El peor lote entrante tendrá una tasa promedio de defectos (p) menor que (k 1 /k 2 ).
p<k 1 /k 2
En este caso: Sin control de entrada. Se debe confiar totalmente en la inspección en el momento de probar los componentes.
Explicación, Sergey P. Grigoryev:
Derivación de la fórmula Condición 1, cuando el costo total de corregir todas las unidades con piezas defectuosas del lote entrante (N×p×k 2 ) será menor que el costo de inspeccionar el 100% de las piezas entrantes (N×k 1 ).
(N) - tamaño del lote entrante de piezas, unidades, con la proporción de piezas defectuosas (p):
N×p×k 2 <N×k 1
reducir la expresión a:
p×k 2 <k 1
Entonces:
p<k 1 /k 2
Condición 2:
El mejor lote entrante tendrá una proporción de artículos defectuosos (p) mayor que (k 1 /k 2 ).
p>k 1 /k 2
En este caso: 100% control de entrada. Y realizar control en el punto de prueba de productos terminados.
Explicación, Sergey P. Grigoryev:
Derivación de la fórmula Condición 2, cuando el costo total de corregir todas las unidades con piezas defectuosas del lote entrante (N×p×k 2 ) será mayor que el costo de inspeccionar el 100% de las piezas entrantes (N×k 1 ).
(N) - tamaño del lote entrante de piezas, unidades, con la proporción de piezas defectuosas (p):
N×p×k 2 >N×k 1
reducir la expresión a:
p×k 2 >k 1
Entonces:
p>k 1 /k 2
(k 1 /k 2 ) - calidad de equilibrio o punto de equilibrio.
(k 2 ) siempre será mayor (k 1 );
por lo tanto, la relación (k 1 /k 2 ) estará entre 0 y 1.
Si aplica la regla de la Condición 2 en una situación en la que se debe aplicar la regla de la Condición 1, entonces el costo total será máximo. Lo contrario también es cierto."
Ejemplo (Sergey P. Grigoryev)
Dado:
p (proporción promedio de artículos defectuosos en el lote de piezas entrante) = 0,05;
k 1 (costo de la inspección entrante de una pieza) = 100,00 ₽;
k 2 (el costo de desmantelar, reparar, volver a ensamblar y volver a probar una unidad que falló debido a una pieza defectuosa que entró en producción) = 1000,00 ₽;
lote de entrada = 1.000,00 unidades.
Condición 1: p<k 1 /k 2 - Sin control de entrada.
Condición 2: p>k 1 /k 2 - 100% control de entrada.
Cálculos
p = 0,05
k 1 /k 2 = 100,00 ₽ / 1.000,00 ₽ = 0,10
0,05 < 0,10
p<k 1 /k 2 - corresponde a la Condición 1 - Sin control de entrada.
Solución
Selecciona el plan “Sin control”.
Comprobando la solución
El costo del control 100% en la entrada será:
1.000 unidades×100,00 ₽=100.000,00 ₽
El coste del paso de materiales defectuosos será:
1.000 unidades×0,05×1000,00 RUR=50.000,00 RUR
En consecuencia, permitir la producción de una pieza defectuosa, en este caso, con el posterior desmontaje, reparación, reensamblaje y prueba de una unidad que falló debido a que una pieza defectuosa entró en producción, costará efectivamente 50.000,00 menos que el 100% de la inspección entrante ₽.
"Por lo tanto, un estado de control estadístico tiene una clara ventaja. Para saber si el flujo de lote entrante cumple con la Condición 1 o la Condición 2 o está en un estado que bordea el caos, sólo es necesario realizar un seguimiento del control estadístico y la tasa promedio de defectos usando gráficos creados sobre la base de pequeñas pruebas en curso (como en cualquier caso), preferiblemente en colaboración con el proveedor y en sus instalaciones."
Otras condiciones observadas en la práctica (Edwards Deming)
Una posición intermedia de la distribución con una desviación moderada de la controlabilidad estadística.
Analizaremos ahora dos tipos de situaciones intermedias para la distribución de la proporción de artículos defectuosos en los lotes entrantes. Quizás, utilizando nuestros propios gráficos de control, o los gráficos del proveedor, o los gráficos mantenidos conjuntamente, podamos predecir que sólo una pequeña parte de la distribución caerá a la derecha del punto de equilibrio. Para este caso podemos adoptar una regla de “no control”. Esta regla nos permitirá acercarnos al mínimo de los costos totales promedio, siempre que la parte de la distribución que se encuentra a la derecha del punto de equilibrio sea pequeña.
La situación opuesta: sólo una pequeña parte de la distribución de la proporción de productos defectuosos en los lotes entrantes se encuentra a la izquierda del punto de equilibrio. Sabiendo esto, puede aceptar con seguridad la regla del control del 100% de los lotes entrantes.
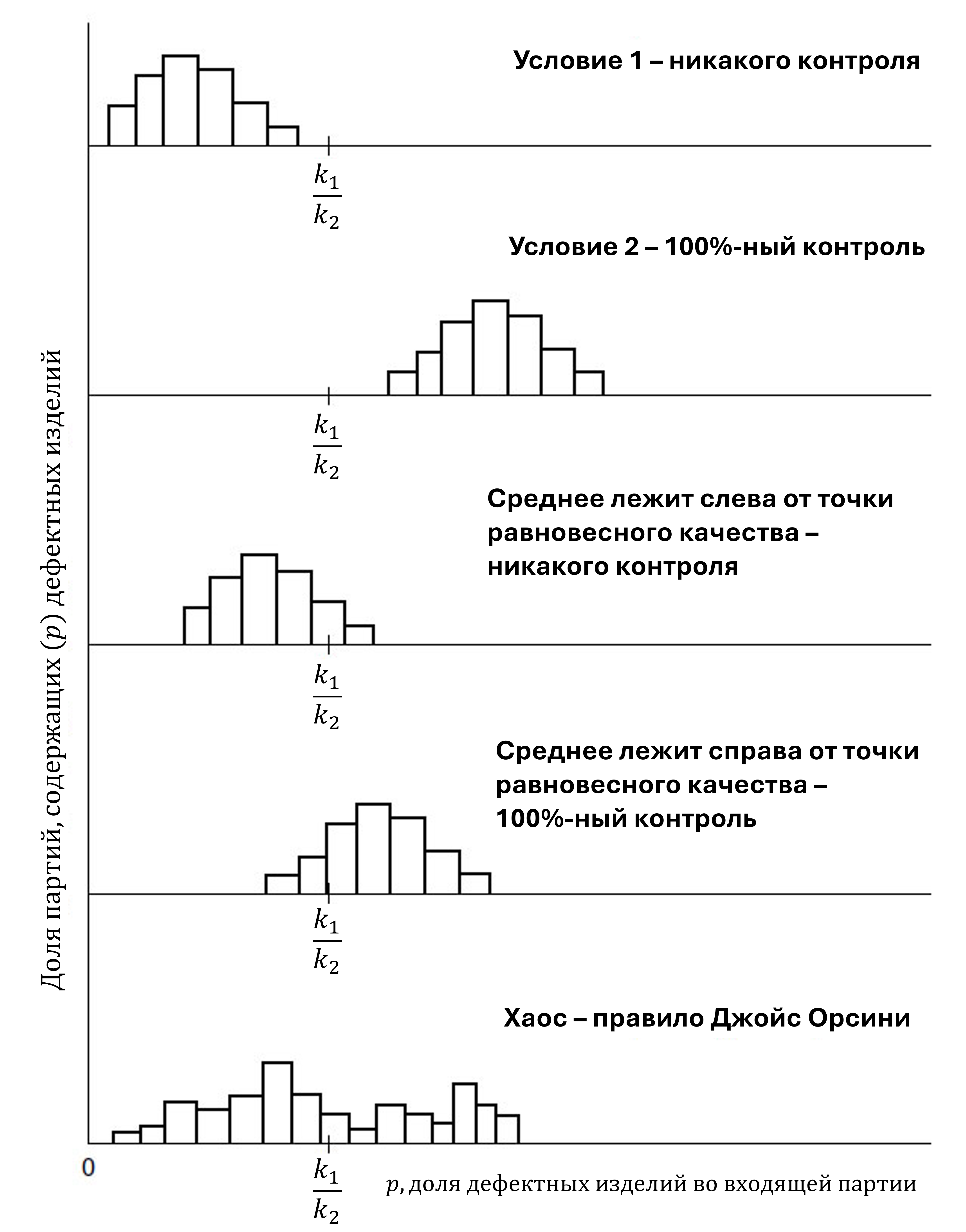
Arroz. 1. Posibles situaciones al recibir productos entrantes en lotes.
El punto B es el punto de equilibrio de calidad, en el que p = k
1
/k
2
. Fuente:
[2]
Edwards Deming, fuera de la crisis
Tendencia en la proporción de productos defectuosos en los lotes entrantes
Supongamos que se ha formado una tendencia hacia un aumento en la proporción de productos defectuosos. Hoy estamos en la Condición 1 y no tenemos control, pero (p) depende del tiempo y aumenta, quizás a un ritmo constante y quizás de manera irregular. En dos días entraremos en la zona de Condición 2: hemos sido advertidos. Los gráficos de control del proveedor o los nuestros revelarán una tendencia, si existe. Este problema se puede resolver fácilmente.
Problemas causados por el cambio entre diferentes proveedores
Debido a cambios en las fuentes de materiales en la entrada del sistema, siempre surgen problemas. Limitémonos a considerar dos fuentes. Si ambas fuentes están bien o moderadamente controladas estadísticamente y pueden separarse entre sí, entonces, en principio, cada fuente satisface la Condición 1 o la Condición 2, dependiendo de si la media de esa fuente cae a la izquierda o a la derecha del punto de equilibrio. Esta idea es simple en palabras, pero puede resultar difícil de implementar en algunas plantas.
Si los materiales de dos fuentes se mezclan homogéneamente en proporción constante, y si ambas fuentes exhiben suficiente control estadístico, entonces los lotes mezclados pueden considerarse como una mezcla binomial, cuyo costo de control promedio mínimo se puede lograr usando el método todo o nada. regla.
Los materiales de dos fuentes plantean problemas adicionales a la producción. Una mezcla homogénea de materiales de dos fuentes es el peor escenario para un director de fabricación.
El primer paso es reducir el número de proveedores a uno. Si un producto de calidad variable es suministrado por una sola fuente, entonces el proveedor y su cliente deben trabajar juntos para mejorarlo, con el objetivo de cumplir la Condición 1 y, en última instancia, lograr cero defectos.
Estado de caos
Decidir qué hacer en una situación en la que la posición de la distribución fluctúa ligeramente acercándose o alejándose del punto de equilibrio es relativamente fácil.
Cerca del punto de equilibrio, realmente no importa si tenemos el 100% de control o ningún control. Yo elegiría un control del 100% para recopilar información lo más rápido posible. Si no podemos afirmar que la calidad de los materiales entrantes se encuentra predominantemente a la derecha o a la izquierda del punto de equilibrio, sino que, por el contrario, fluctúa ampliamente, pasando por el punto de calidad de equilibrio, entonces estamos en un estado de caos.
1. Esta situación inaceptable puede surgir cuando un material con alta variabilidad y calidad impredecible proviene de una sola fuente.
2. Tal variación alrededor del punto de calidad de equilibrio puede resultar de la obtención de material de dos o más fuentes de calidad muy variable. En este caso, el cambio de una fuente a otra se realiza de forma incontrolable, sin una secuencia pensada. Deberíamos salir de este estado lo más rápido posible y pasar a la Condición 1. Pero los lotes siguen llegando y tenemos que hacer algo con ellos. ¿Cómo debemos abordarlos?
Si cada lote viniera con una etiqueta que nos dijera la proporción de artículos defectuosos que contiene, no habría problema. Lograríamos un costo total promedio mínimo colocando cada lote, uno tras otro, a la derecha o izquierda del punto de equilibrio y aplicando la regla del todo o nada de un lote a otro.
Pero los lotes no están marcados. Sin embargo, en un estado de caos existe cierta correlación entre la calidad de los productos de la muestra y el resto del lote. Por lo tanto, en un estado de caos, puede probar muestras y, utilizando alguna regla, decidir si enviar la pieza restante a producción por completo o rechazarla.
El muestreo, por muy bien que se utilice, hará que algunos lotes terminen en el lado equivocado del punto de equilibrio, con la consecuencia de maximizar los costos totales del lote mal identificado.
En un estado de caos, uno podría inclinarse hacia un control del 100%. Esta decisión tiene cierto sentido.
Nunca te quedes sin información
La regla de no control de entrada no significa conducir en la oscuridad con las luces apagadas. Todos los materiales entrantes deben revisarse (posiblemente omitiendo algunos lotes) para obtener información y comparar la entrega real con las notas de envío del proveedor, la inspección de las pruebas del proveedor y los cuadros de control adjuntos. Si hay dos proveedores, mantenga registros para cada uno por separado.
El siguiente consejo es acudir a un proveedor para cada producto basándose en una relación a largo plazo y trabajar con ellos para mejorar la calidad entrante.
Pruebas destructivas
La teoría anterior se basa en pruebas no destructivas de un prototipo. Algunas pruebas son destructivas; Destruyen la muestra controlada. Un ejemplo es la vida útil de una bombilla, el número de calorías térmicas producidas al quemar un pie cúbico de gas, o el tiempo de funcionamiento de una mecha, o probar el contenido de lana de un trozo de tela. Rechazar todo el lote no tendría sentido, ya que no habría nada que transferir a producción.
Evidentemente, para los ensayos destructivos, la única solución es alcanzar un estado de control estadístico en la producción de las piezas para poder fabricarlas correctamente de inmediato. Esta solución es la mejor para pruebas tanto destructivas como no destructivas.
Posibilidad de montaje defectuoso de muchas piezas.
En los apartados anteriores hablamos de productos sencillos compuestos por una sola pieza. Algunas piezas pueden requerir una inspección del 100% para minimizar el costo total. Una vez probados, no harán que falle el conjunto (conjunto). Las piezas restantes no serán probadas, y la pieza defectuosa, si entra en producción, provocará una falla. Digamos que tenemos dos partes no probadas.
Dos piezas no probadas tienen partes defectuosas p 1 y P 1 . Entonces la probabilidad de que el conjunto falle será igual a:
pr (se negará) = 1 – Pr (no se negará) = 1 – (1 – pag 1 )(1-p 2 ) = pag 1 +p 2 -pag 1 pag 2
Si ambos valores de p 1 y P 2 -pequeña, entonces esta probabilidad será cercana al valor:
pr (se negará) =p 1 +p 2
Una forma sencilla de escribir la probabilidad de falla de cualquier número de piezas es utilizar diagramas de Venn (descritos en cualquier libro sobre teoría de la probabilidad).
Siempre que todos los p i pequeño. La generalización a m partes da:
pr (se negará) =p 1 +p 2 + … + p metro
Por tanto, la probabilidad de falla aumenta a medida que aumenta el número de piezas. Una radio puede tener 300 piezas, aunque este número dependerá de cómo las cuentes. Un automóvil puede tener 10.000 piezas, nuevamente dependiendo de cómo se cuente. ¿La radio de un auto es de una pieza o 300? ¿La bomba de combustible es 1 pieza o 7? No importa lo que piense, la cantidad de piezas en un solo ensamblaje puede resultar abrumadora.
` Pero hay otro problema: k 2 (el costo de corregir un conjunto defectuoso) aumenta a medida que aumenta el número de piezas. Cuando falla un ensamble, ¿qué pieza tiene la culpa? Es muy fácil diagnosticar erróneamente. Además, de dos piezas, ambas pueden estar defectuosas.
Para productos que constan de muchas partes:
1. Podemos permitir que sólo unas pocas piezas cumplan la Condición 2 (100% de control); de lo contrario, el costo del control será excesivo.
2. Para otras piezas, sólo se acepta una calidad cercana a cero defectos.
Conjuntos de componentes complejos.
Posibles ahorros al crear subsistemas auxiliares. En la teoría anterior, el costo k 2 normalmente aumenta (posiblemente un aumento de 10 veces) con cada paso del proceso y puede alcanzar valores muy altos durante el ensamblaje final. A veces se pueden evitar costes innecesariamente elevados creando subsistemas que se mueven a lo largo del flujo ensamblado y forman el producto final. Algunos subsistemas, que han pasado por el control y requieren reemplazos y ajustes menores, forman un nuevo punto de partida. Costo k 2 Ahora será el costo de monitorear y ajustar el subsistema. La teoría, junto con registros útiles de experiencia, puede demostrar que algunos subsistemas no necesitan ser probados en absoluto, mientras que otros deberían estar sujetos a un control del 100% para evitar aumentos de costos a medida que avanza el proceso. La teoría presentada en este capítulo le permitirá tomar la decisión correcta.
Nuestro objetivo en las secciones anteriores es mostrar que hay maneras de minimizar los costos y maximizar las ganancias si se sigue la teoría correcta.
Al mismo tiempo, hacemos todo lo posible para eliminar completamente los productos defectuosos del proceso. Esto lo hacemos sistemáticamente comparando los resultados de nuestras pruebas con los del proveedor y aplicando métodos estadísticos adecuados, como los gráficos X y R (gráficos de control de Shewhart).
La cooperación fructífera con el proveedor de piezas, especialmente las críticas, y las pruebas y ajustes exitosos de los subsistemas reducen todos los problemas importantes durante la inspección final de los sistemas a eventos excepcionales.
El material entrante es un subproducto para el proveedor.
Cuando un material crítico para el cliente de un proveedor puede ser un subproducto que represente menos del 1% de su negocio. No se puede esperar que el proveedor asuma el costo y el riesgo de instalar equipos para mejorar el producto.
Una posible recomendación es considerar este material como mineral de hierro u otros insumos altamente variables y no purificados. Instale su propio sistema de limpieza de materiales o utilice los servicios de una empresa externa. Este plan es eficaz en algunos casos.
Dificultades para detectar defectos raros.
Los defectos raros son difíciles de detectar. A medida que disminuye la proporción de productos defectuosos, resulta cada vez más difícil determinar qué tan pequeño es el número. No es posible detectar todos los defectos mediante la inspección, especialmente cuando son raros, y esto es válido tanto para la inspección visual como para la automática. No hay razón para confiar más en un fabricante que afirma tener sólo 1 defecto entre 10.000 que en uno que afirma tener 1 defecto entre 5.000 productos. En ambos casos, esta proporción es difícil de estimar.
Por lo tanto, si (p) fuera igual a 1/5000 y si el proceso estuviera en un estado controlado estadísticamente, entonces se tendrían que inspeccionar 80.000 piezas para encontrar 16 defectuosas.
Serguéi P. Grigoriev:
5000×16=80000
Estos datos darían una estimación de la tasa de defectos promedio de p = 1/5000 para un proceso de producción con un error estándar de σ = √16 = 4. Esta estimación de la tasa de defectos es imprecisa, a pesar de la dificultad de monitorear muchos 80.000 piezas. Surge la pregunta: ¿el proceso se mantuvo estable durante la producción de 80.000 piezas? En caso negativo, ¿cuál es el significado del número 16 productos defectuosos? Pregunta dificil.
Serguéi P. Grigoriev:
En este caso, si el proceso del proveedor está en un estado controlado estadísticamente, se supone que opera alrededor del valor promedio c = 16 defectos para lotes en forma de subgrupos de 80.000 piezas de tamaño con los valores del superior (VKG , UCL) y límites de control inferiores (NKG, LCL) Gráficos C: UCL, LCL = c ±3σ o UCL, LCL = c ±3√c, lo que da como resultado una dispersión de valores alrededor del promedio (c=16) dentro de ±12.
Las fórmulas se pueden encontrar en GOST R ISO 7870-1-2011 (ISO 7870-1:2007), GOST R ISO 7870-2-2015 (ISO 7870-2:2013) - Métodos estadísticos. Gráficos de control de Shewhart [once] .
Para calcular (σ), Deming utiliza un gráfico C del número de defectos por área de definición constante igual a 80.000 piezas.
¿Por qué 16? El valor promedio (16) permite un fácil cálculo del valor (σ) para el gráfico C y proporciona límites de control superior e inferior.
Por lo tanto, para que un proveedor reclame tal tasa de defectos (1/5000) requiere una comprensión de la estabilidad de su proceso de producción, que sólo puede confirmarse utilizando gráficos de control de Shewhart, y el gráfico de control debe construirse, por ejemplo, a una mínimo de ocho puntos, donde cada punto es el número de defectos por lote de 80.000 piezas con posibles valores enteros de 4 a 28 defectos distribuidos en regla de oro alrededor del promedio: 16 defectos por lote de 80.000 piezas.
¿Por qué fue imposible realizar estas operaciones matemáticas simples con el valor promedio de defectos c = 1 para un dominio de definición constante de 5000 partes? Sí, porque no podrá obtener puntos de números enteros del número de defectos en el gráfico de control por debajo del valor promedio c=1, excepto cero. Aunque matemáticamente es fácil obtener un número decimal en los cálculos, por ejemplo, = 0,3, ¿cómo imagina la posibilidad de obtener en condiciones reales el número de defectos de 0,3 en un lote (subgrupo) probado?
Hay ejemplos en los que en millones de piezas no hay ni un solo fallo, o su número es muy pequeño o faltan 10 mil millones. Ningún control de los productos terminados ayudará a obtener la información requerida cuando la proporción de productos defectuosos es tan pequeña. La única forma posible de saber qué sucede ante demandas tan extremas es utilizar gráficos de control con mediciones reales de las piezas durante el proceso. Cien observaciones, como 4 elementos seguidos 25 veces al día, producirían 25 puntos de muestra para los gráficos X y R de medias y rangos de subgrupos. Los gráficos de control de Shewhart mostrarían si el proceso avanza sin cambios o si ha ocurrido una falla en alguna parte y la producción de varios productos debe detenerse hasta que se descubra la causa. Una vez encontrado el motivo, puede decidir rechazar todo el conjunto de productos durante un período determinado u omitir algunos productos. Las capacidades cada vez mayores de los gráficos de control XbarR de subgrupos de promedio y rango son cada vez más obvias.
Sergey P. Grigoryev: Donald Wheeler en el artículo ¿Gráficos de control para datos alternativos (recuentos): gráfico p, gráfico np, gráfico C y gráfico u o un gráfico XmR de valores individuales? refuerza esta recomendación de Edwards Deming:
"Dado que rara vez tiene sentido utilizar cantidades discretas (recuentos) cuando se pueden obtener resultados de medición, el uso de atributos generalmente se limita a situaciones en las que se pueden contar los "errores". Sin embargo, definir un "error" suele plantear una gran dificultad. La principal dificultad para definir "blooper" es un problema. definiciones operacionales ".
Usando reservas
A veces es posible y razonable al diseñar equipos complejos colocar dos o más piezas en paralelo, de modo que si una de ellas falla, la otra automáticamente asumirá sus funciones. Dos partes paralelas, cada una con una tasa de defectos promedio p i , son equivalentes a uno con una tasa promedio de defectos igual a p i ². Si, por ejemplo, p i =1/1000, entonces p i ²=1/1000000.
Por supuesto, las restricciones de peso y tamaño pueden impedir el uso de la redundancia.
Hay otras preocupaciones: ¿funcionará la parte de respaldo cuando sea necesario? Quizás la mejor solución sea una alta fiabilidad en una sola pieza.
Conclusión
No se tolerarán materiales ni mano de obra defectuosos en el proceso de fabricación. La teoría descrita anteriormente nos enseña lo importante que es no tolerar materiales defectuosos en ninguna etapa de la producción. El producto de una operación es el material de entrada para la siguiente. Un material defectuoso, una vez producido, sigue siendo defectuoso hasta que se descubre el defecto, aunque afortunadamente, más adelante en las pruebas, la corrección y el reemplazo no serán baratos.
El estado de controlabilidad estadística tiene una clara ventaja. Para saber si el flujo de lote entrante cumple con la Condición 1 o la Condición 2 o se encuentra en un estado que bordea el caos, sólo es necesario monitorear el control estadístico y el porcentaje promedio de artículos defectuosos usando gráficos de control de Shewhart construidos a partir de pruebas continuas de muestras pequeñas (como en cualquier caso), preferiblemente en cooperación con el proveedor y en su territorio.
Excepciones
Muchos materiales de entrada no siguen la teoría descrita anteriormente. Por ejemplo, un tanque de metanol después de agitarlo con una manguera de aire. Una muestra de metanol tomada de casi cualquier parte del tanque será casi la misma. Sin embargo, las empresas químicas toman muestras de metanol en varios niveles. Quizás un ejemplo más cercano sea probar un trago de ginebra o whisky. Estamos de acuerdo en que no importa de dónde tomemos la ración: de arriba, de la mitad de la botella o de abajo.
Explicación Sergey P. Grigoryev: El párrafo anterior se refiere a casos excepcionales en los que el resultado del control de la muestra se puede atribuir a todo el lote.
El calentamiento de altos hornos crea problemas y es otro ejemplo al que no se aplica la teoría de este capítulo. El calentamiento no es uniforme. Algunas empresas toman pequeñas muestras de cada embotellado. Estas muestras, si se analizan, proporcionan datos para un diagrama de proceso que podría mostrar variaciones en la calidad desde el primer molde hasta el último, proporcionando pistas para mejorar.
Explicación de Sergey P. Grigoryev: El párrafo anterior trata de casos excepcionales en los que el proceso es, por definición, heterogéneo en diferentes etapas del proceso con la posibilidad de tomar una muestra de cada etapa; en tales casos, para analizar la variación entre diferentes lotes (piezas fundidas), es necesario utilizar un mapa XmR de control de valores individuales.
Ver solución de código abierto: Problemas del uso de tablas para el control de calidad de aceptación aleatoria. .