Formas correctas e incorrectas de utilizar los campos de tolerancia. ¿Deberíamos clasificar los productos según márgenes de tolerancia para defectuosos y no defectuosos, o deberíamos intentar personalizar el proceso?
Artículo: [26] DONALD J. WHEELER: "Formas correctas e incorrectas de utilizar las especificaciones. ¿Clasificar o ajustar?"
Traducción, notas y material gráfico adicional con explicaciones: Director Científico del Centro AQT
Serguéi P. Grigoriev
, utilizando materiales que Donald Wheeler le proporcionó amablemente.
El libre acceso a los artículos no disminuye en modo alguno el valor de los materiales contenidos en ellos.
En este artículo, veremos la historia y el propósito de los campos de tolerancia, y veremos dos formas comunes de usarlos en la práctica. Usando ejemplos simples, ilustraré las formas correctas e incorrectas de usar los campos de tolerancia (especificaciones).
Nota Sergey P. Grigoryev: El artículo demuestra claramente que el ajuste operativo del proceso por parte del operador de la máquina en relación con los campos de tolerancia sólo tiene sentido para procesos que son inestables y/o no centrados en el campo de tolerancia, mientras que la corrección de valores estables y Los procesos bien centrados en el campo de la tolerancia conducen a una variabilidad aún mayor (una mayor dispersión de datos alrededor de la media), lo que priva a los trabajadores de comprender "¿qué está sucediendo?" cuando intenta mejorar la calidad de las piezas que produce.
Voz del cliente
Hace unos 220 años, Eli Whitney creó una desmotadora de algodón con piezas reemplazables. El uso de piezas intercambiables supuso un avance tecnológico de la época. Poco después de su éxito con la desmotadora de algodón, Whitney recibió un contrato para suministrar al ejército estadounidense mosquetes con piezas intercambiables. En un intento por producir un gran número de piezas que pudieran usarse indistintamente, descubrió inmediatamente un hecho que ha perseguido a todas las producciones desde entonces: no hay dos cosas iguales.
Entonces, en lugar de hacer las cosas iguales, tuvieron que contentarse con hacerlas similares. Una vez que aceptaron esto, inmediatamente surgió la pregunta: “¿Qué tan similares son las partes suficientemente similares?” Para intentar responder a esta pregunta, se crearon condiciones técnicas (campos de tolerancia, especificaciones). Era obvio que se podían tolerar pequeñas desviaciones ya que las piezas seguirían funcionando. Sin embargo, a medida que aumentan las variaciones, llegará un punto en el que será más barato desechar la pieza que intentar utilizarla. Y los campos de tolerancia (especificaciones) estaban destinados a determinar este punto de corte de pérdida.
Hace doscientos años, la economía de la producción en masa era tan grande que se podían tolerar grandes cantidades de desperdicio. En la década de 1840, se inventó la herramienta de calibre (pasa-falla). En la década de 1860, esto se había convertido en el "medidor pasa-no-pasa", que permitía clasificar económicamente grandes cantidades de piezas en piezas buenas y malas. Esta tecnología de la década de 1860 todavía se utiliza en la actualidad. Se crearon campos de tolerancia para separar el producto aceptable del producto inaceptable. Siempre que un flujo de productos contenga elementos no conformes que puedan identificarse mediante pruebas no destructivas, el uso de pruebas al 100 por ciento sigue siendo una estrategia razonable cuando se puede realizar de una manera económicamente viable. Una vez que hayas quemado la tostada, ¿qué puedes hacer además de limpiar los trozos quemados?
Ejemplo
Las figuras 1 y 2 muestran los 100 valores de prueba finales junto con su histograma y el mapa X de Shewhart para los valores individuales. Estos valores se derivan de una operación de fabricación en una de las plantas de mi cliente. Las bandas de tolerancia para estos valores oscilan entre 67 y 71. El histograma muestra que este proceso tiene solo un rendimiento del 34 por ciento, mientras que el mapa X muestra que este proceso opera de manera impredecible. El margen de tolerancia nos permite diferenciar entre artículos conformes y no conformes, pero un rendimiento del 34 por ciento es inaceptable.
¿Necesitas hacer algo?
Un curso de acción popular es tratar de mejorar el resultado mediante la realización de ajustes apropiados en el proceso. Supongamos que podemos ajustar el proceso después de cada resultado de medición de una pieza seleccionada para inspección (prueba) y que cada ajuste afectará los productos producidos posteriormente. Usaremos los límites de tolerancia de 67 y 71 para determinar la zona muerta para nuestros ajustes. Es decir, ajustaremos el proceso sólo cuando recibamos un resultado de prueba inadecuado. Si, digamos, tenemos un resultado de prueba de 65, entonces ajustaremos el proceso hacia arriba en 4 para apuntar el proceso a un valor de tolerancia promedio de 69, y si tenemos un resultado de 75, entonces ajustaremos el proceso hacia abajo en 6. Sin embargo, si el resultado de la prueba es 67, 68, 69, 70 o 71, no haremos ningún cambio en este proceso. A este tipo de ajuste lo llamaremos además "controlador P".
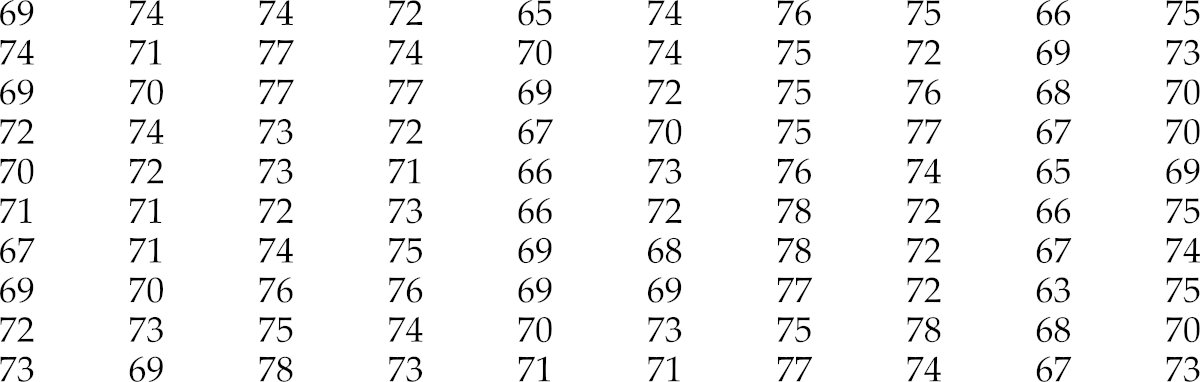
Puede descargar los datos de la lista ordenada en formato CSV para crear su propio gráfico de control XmR: descargar .
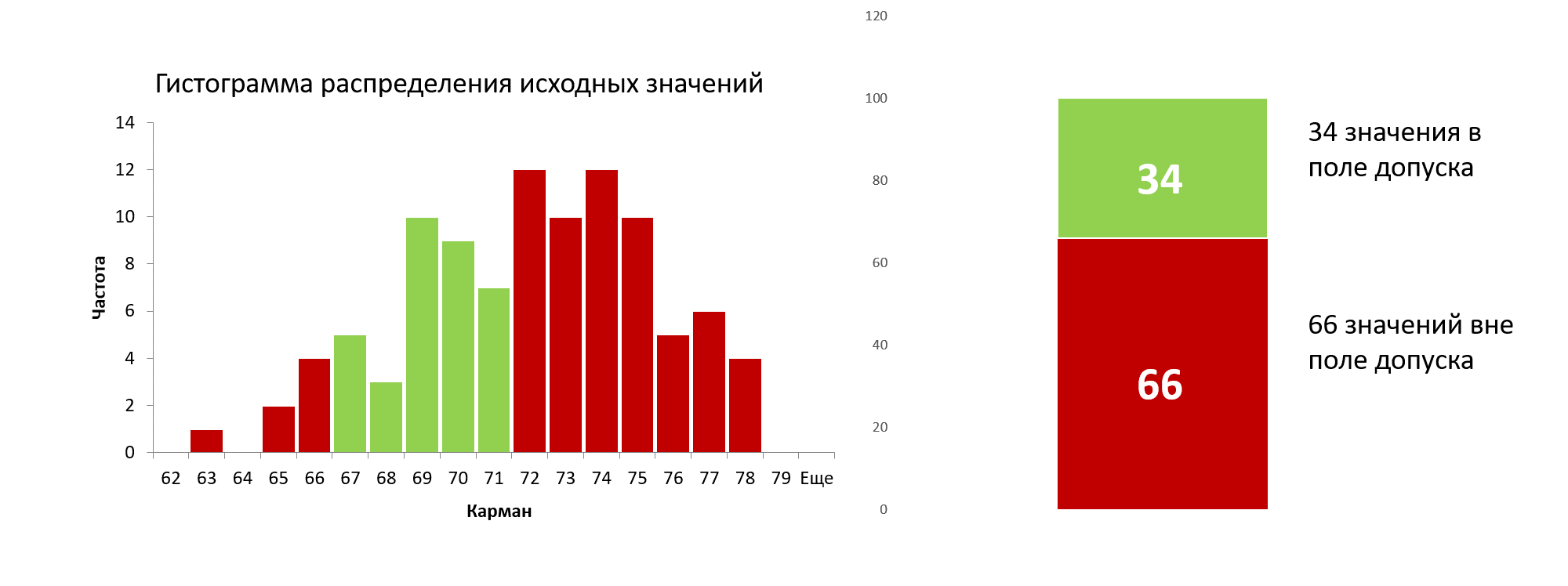
Figura 1: Histograma de la distribución de 100 valores iniciales de un proceso inestable y mal centrado antes del ajuste.
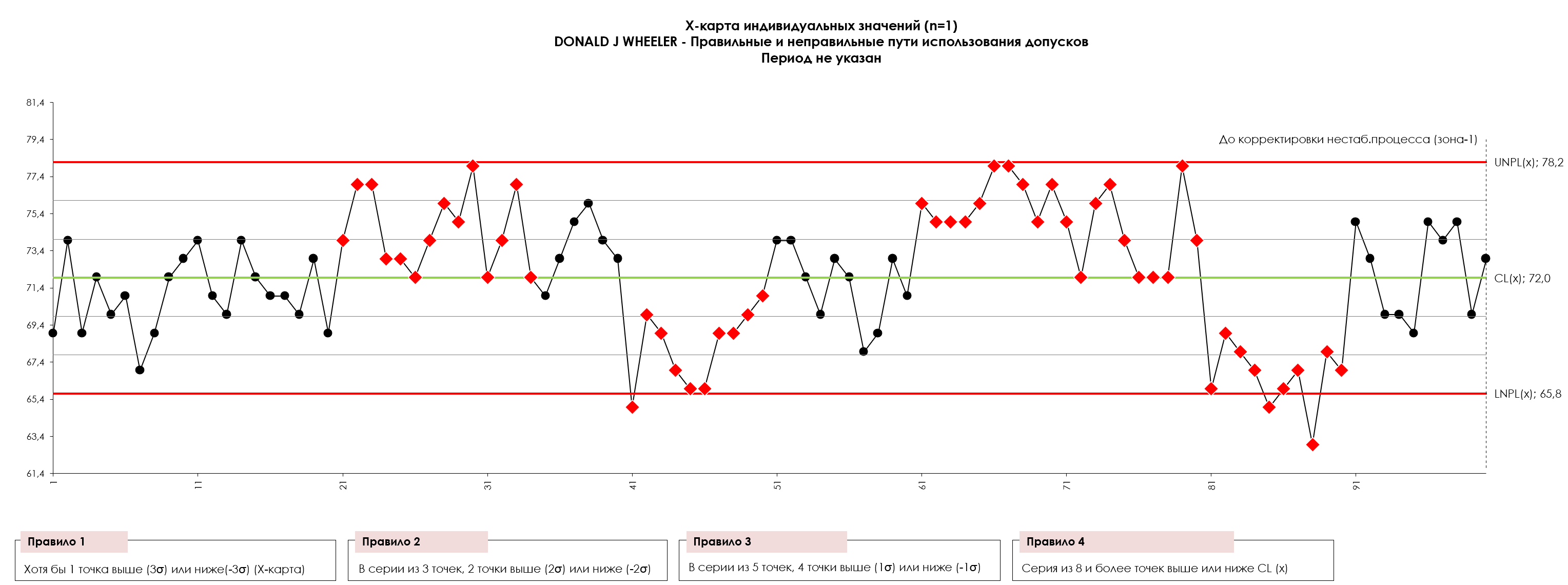
Figura 2: Mapa X de valores individuales (voz de proceso) 100 valores iniciales de un proceso inestable y mal centrado antes de la corrección del operador. Las líneas rojas, respectivamente, son los límites naturales superior e inferior del proceso, la línea verde es la línea central (promedio) del proceso. Los puntos rojos (series de puntos) son señales de la presencia de causas especiales, que indican un estado estadísticamente incontrolable del proceso. El dibujo fue preparado usando nuestro desarrollado. “Gráficos de control de Shewhart PRO-Analyst +AI (para Windows, Mac, Linux)” .
La Figura 2 animada a continuación muestra cómo funcionará el procedimiento de ajuste con los datos originales de la Figura 1. Por ejemplo, un valor inicial de 69 no hará que se ajusten los valores posteriores. Un segundo valor de 74, más un ajuste de cero a la medición anterior, da como resultado un valor ajustado de 74. Esto da como resultado un ajuste de -5 a un objetivo de proceso de 69. Un tercer valor de 69 más un ajuste de medición anterior de - 5 da un tercer valor ajustado de 64. Esto da como resultado un ajuste de +5 valores del siguiente proceso, etc.
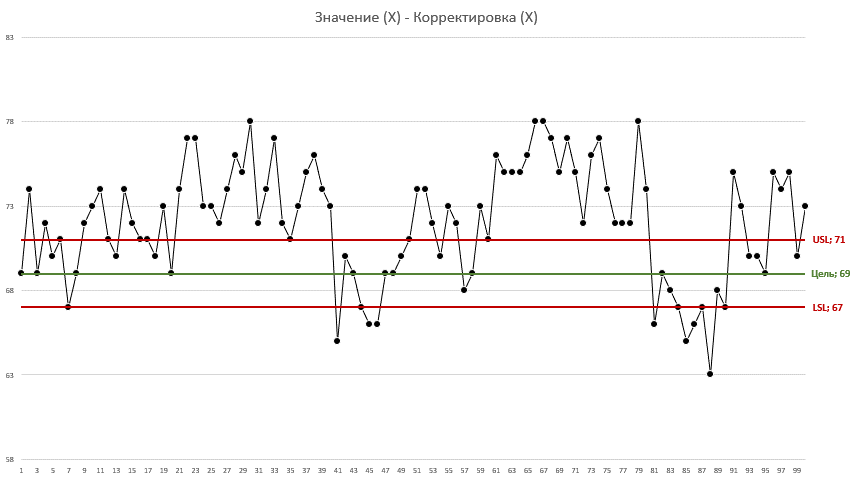
Figura 3: Se corrige la animación del cambio de 100 valores iniciales como un proceso inestable y mal centrado. USL es el límite superior de la tolerancia, Target es el valor nominal del campo de tolerancia, LSL es el límite inferior del campo de tolerancia.
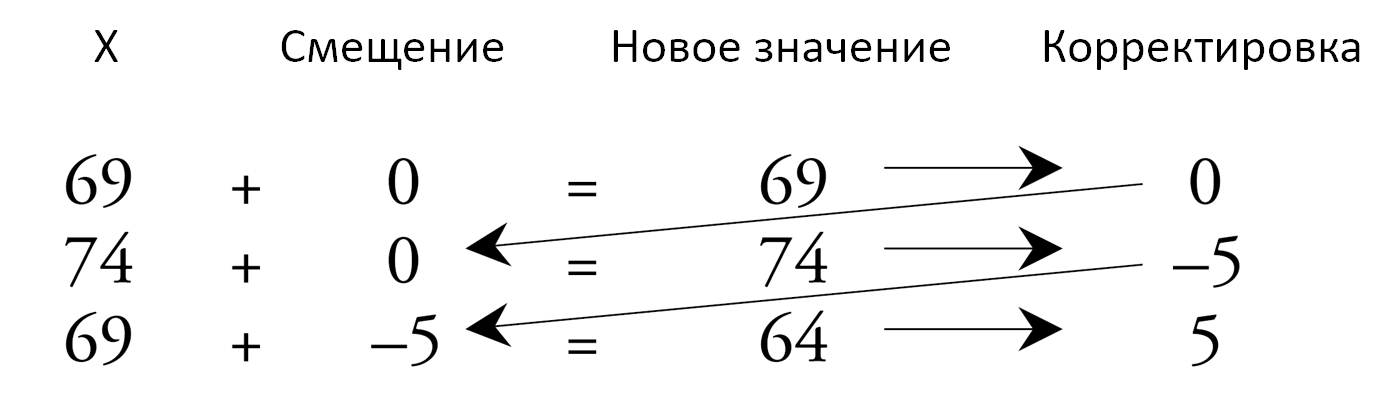
Figura 4: Regla para ajustar el proceso midiendo una pieza “defectuosa”.
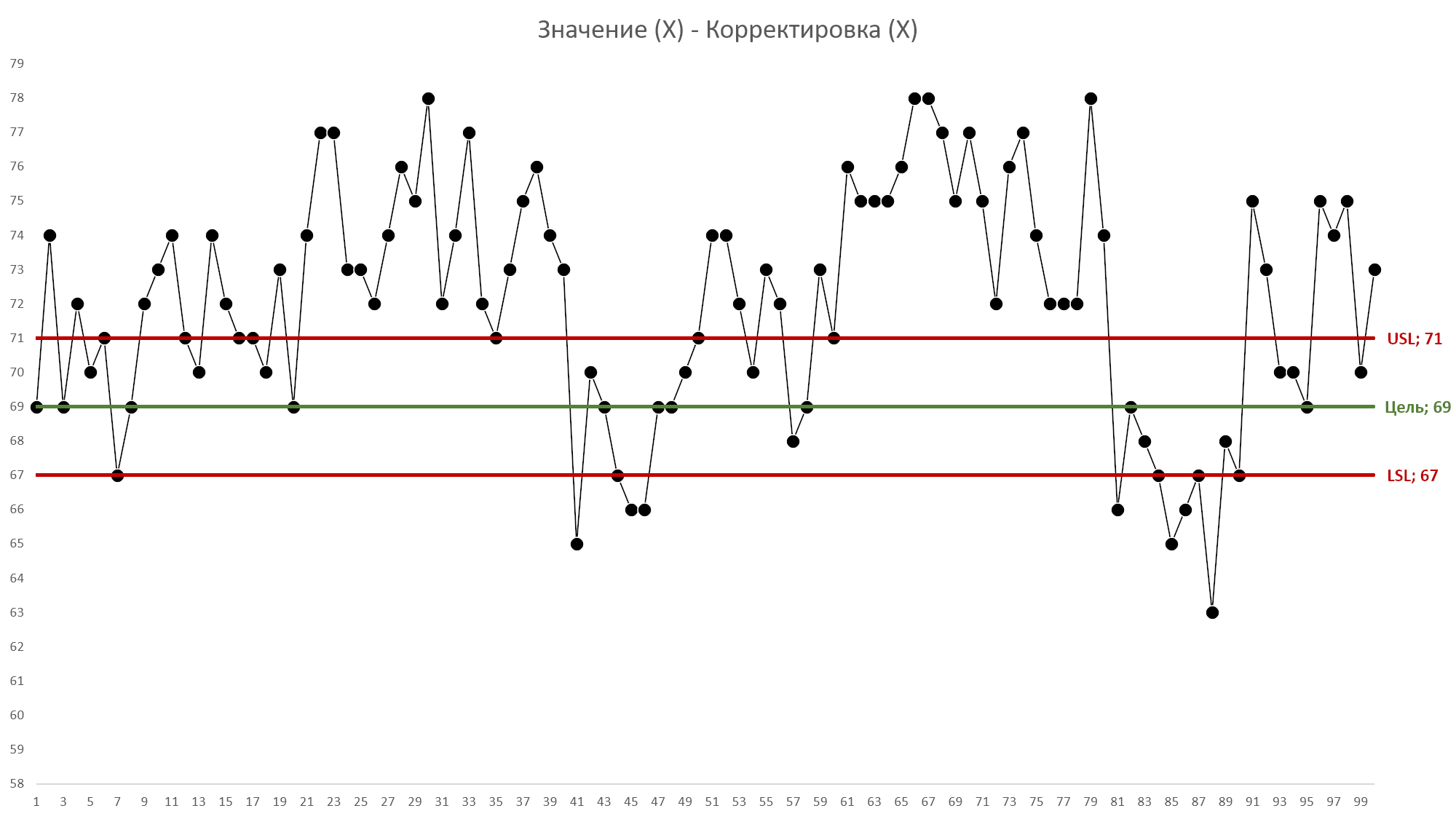
Figura 5: Gráfico de 100 (cien) valores iniciales antes de ajustar un proceso inestable y mal centrado contra campos de tolerancia (voz del cliente). USL es el límite superior de la tolerancia, Target es el valor nominal del campo de tolerancia, LSL es el límite inferior del campo de tolerancia.
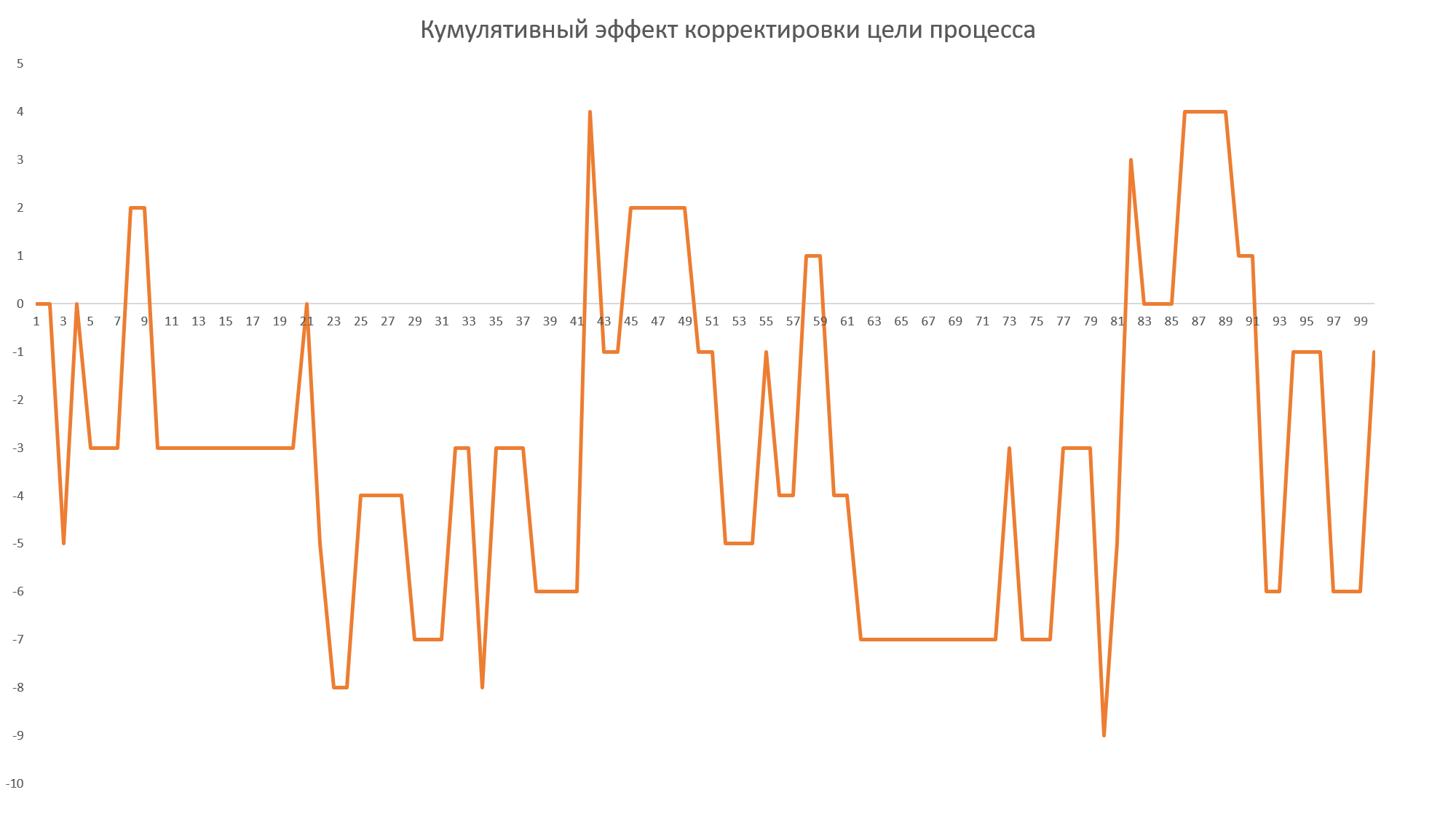
Figura 6: Efecto acumulativo del ajuste de un proceso descontrolado y mal centrado.
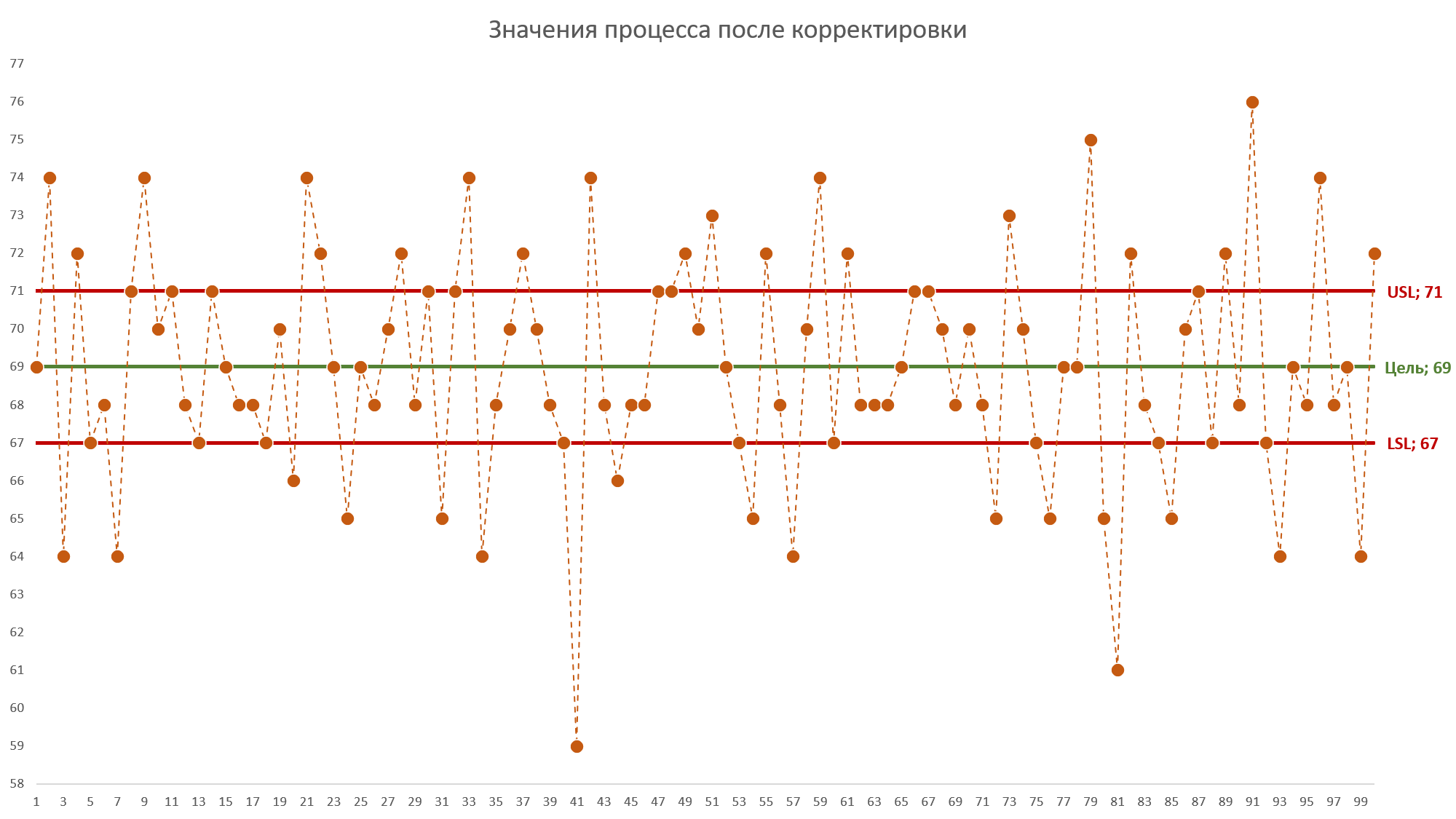
Figura 7: Datos resultantes de un proceso no controlado y mal centrado después de la conversión mediante un controlador P utilizando bandas de tolerancia como banda muerta. USL es el límite superior de la tolerancia, Target es el valor nominal del campo de tolerancia, LSL es el límite inferior del campo de tolerancia.
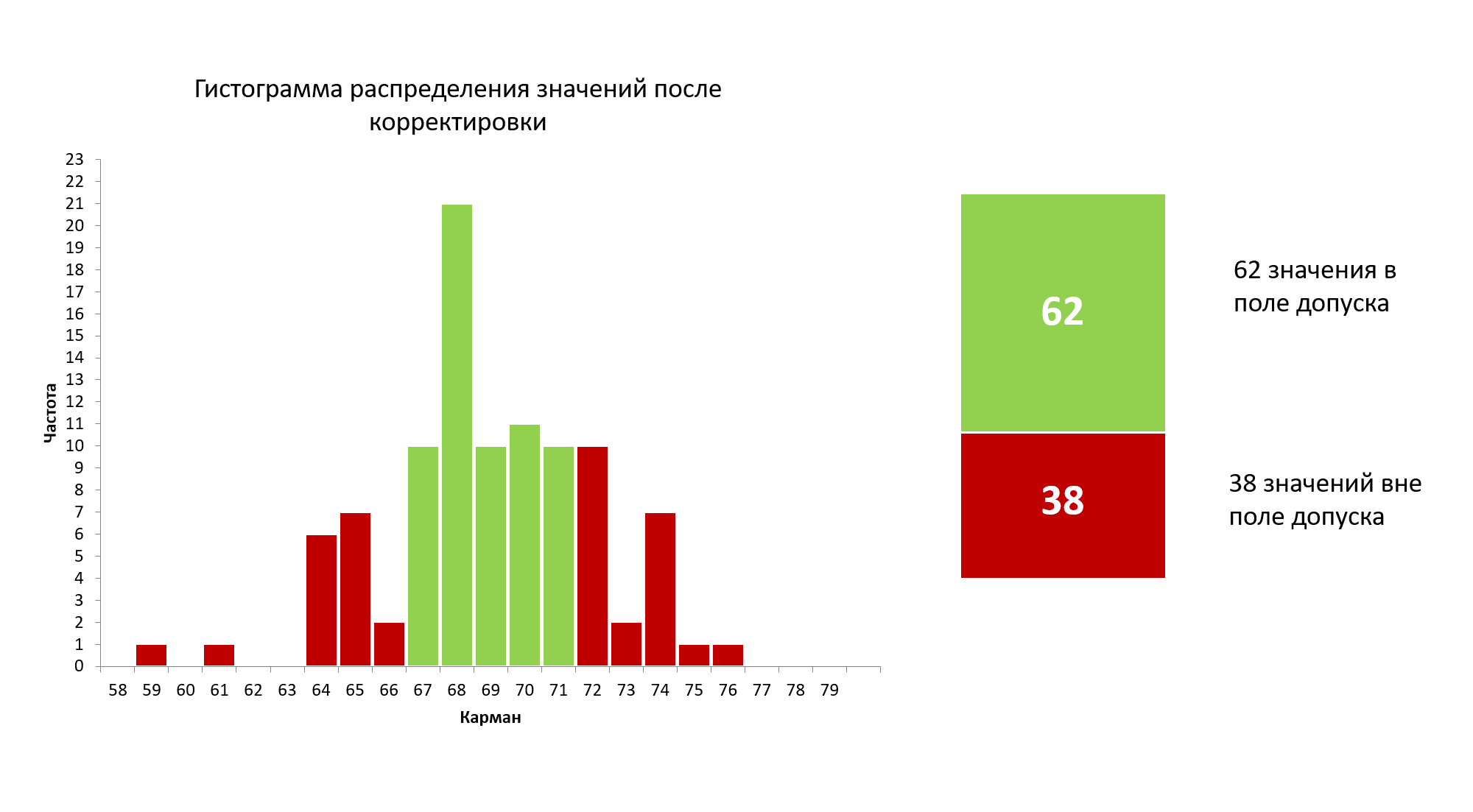
Figura 8: Histograma de la distribución de 100 nuevos valores después de corregir por un proceso inestable y mal centrado.
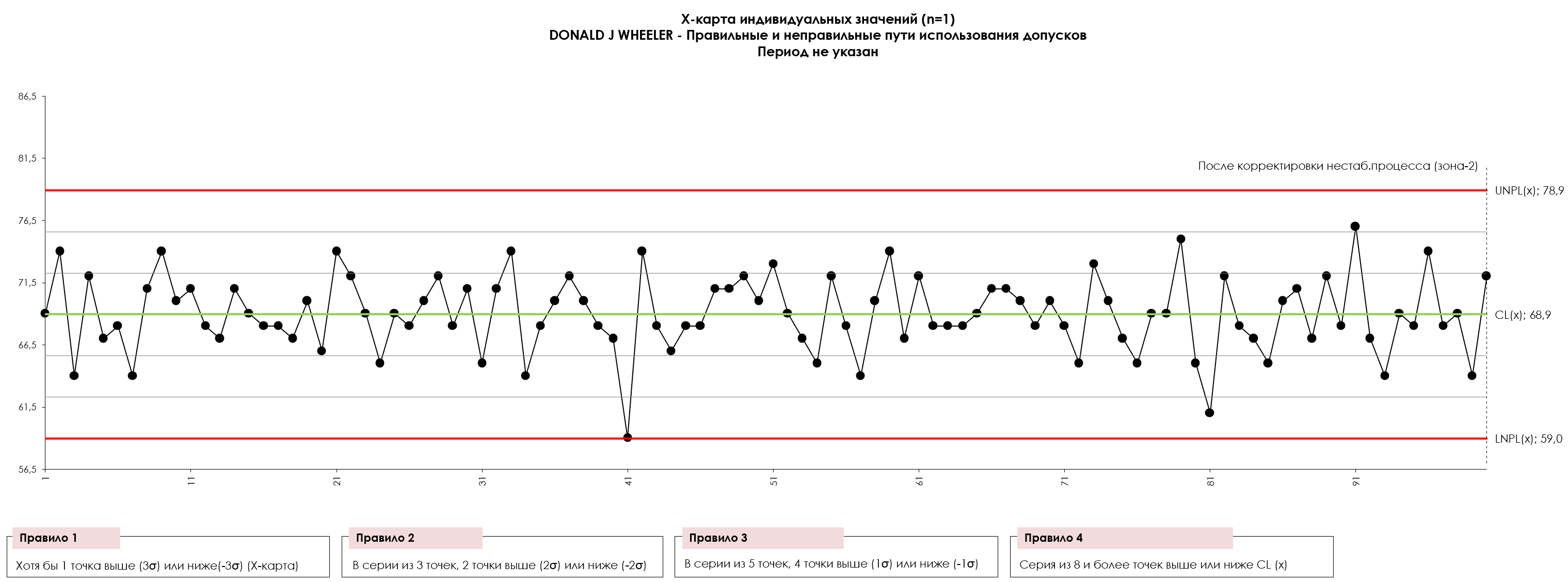
Figura 8.1.: Mapa X de valores individuales (voz de proceso) 100 valores después de la corrección por parte del operador del proceso inestable y sesgado (no centrado) que se muestra en la Figura 2 demuestra un estado estadísticamente estable. El dibujo fue preparado usando nuestro desarrollado. “Gráficos de control de Shewhart PRO-Analyst +AI (para Windows, Mac, Linux)” .
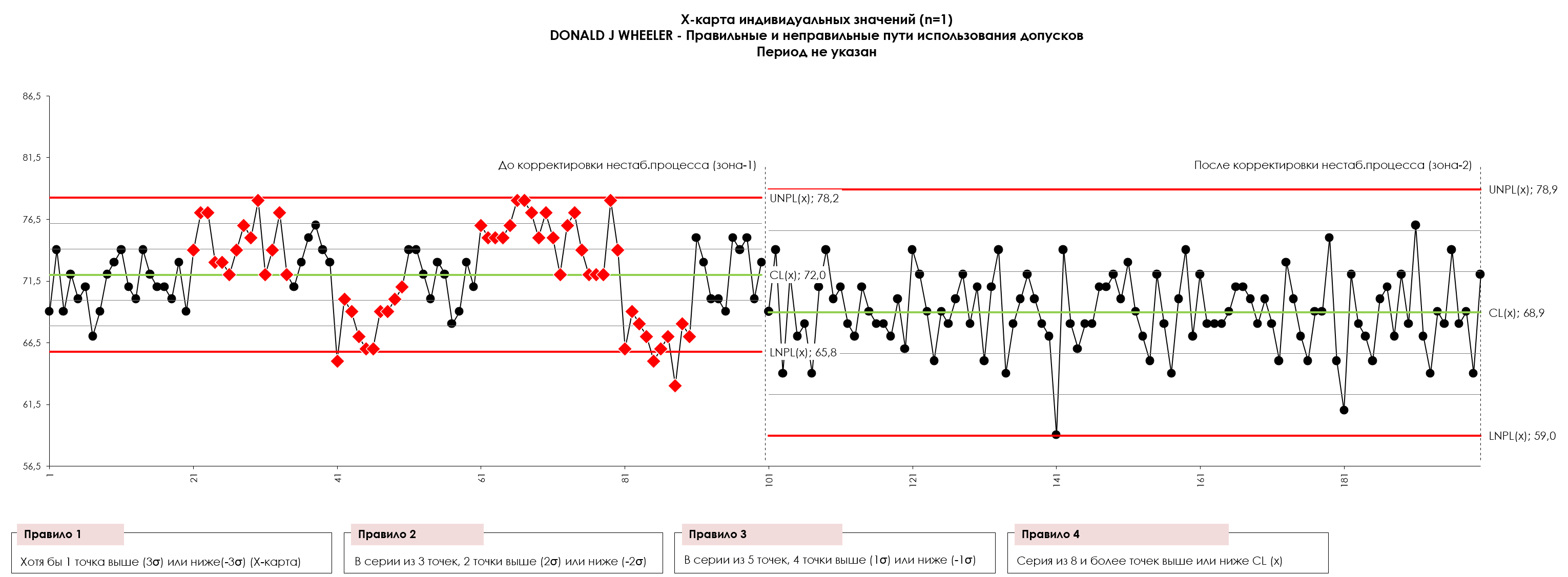
Figura 8.2.: El mapa X de valores individuales (voz de proceso) de 100 valores antes (zona-1) y después (zona-2) de la corrección de un proceso inestable y sesgado (no centrado) demuestra una estabilidad estadística estado. El dibujo fue preparado usando nuestro desarrollado. “Gráficos de control de Shewhart PRO-Analyst +AI (para Windows, Mac, Linux)” .
Entonces, ¿cómo nos las arreglamos? El controlador P que utilizó límites de tolerancia para determinar la zona muerta aumentó el rendimiento del 34 por ciento al 62 por ciento. Una mejora muy impresionante. Esto sucedió porque este proceso no se concentró en la zona de tolerancia y se controló de manera impredecible. Como resultado de estos dos aspectos de los datos mostrados en la Figura 2, muchos de los treinta y dos (32) ajustes fueron realmente necesarios para mejorar y, por lo tanto, el controlador P mejoró el rendimiento.
Sin embargo, un rendimiento del 62 por ciento no era todo lo que el proceso era capaz de conseguir. Podría haber sido mejor. Una vez que identificamos las causas especiales de la variación excepcional que se muestra en la Figura 2 y tomamos medidas para controlar esas causas especiales en la producción, terminamos con el proceso que se muestra en la Figura 9 (a continuación).
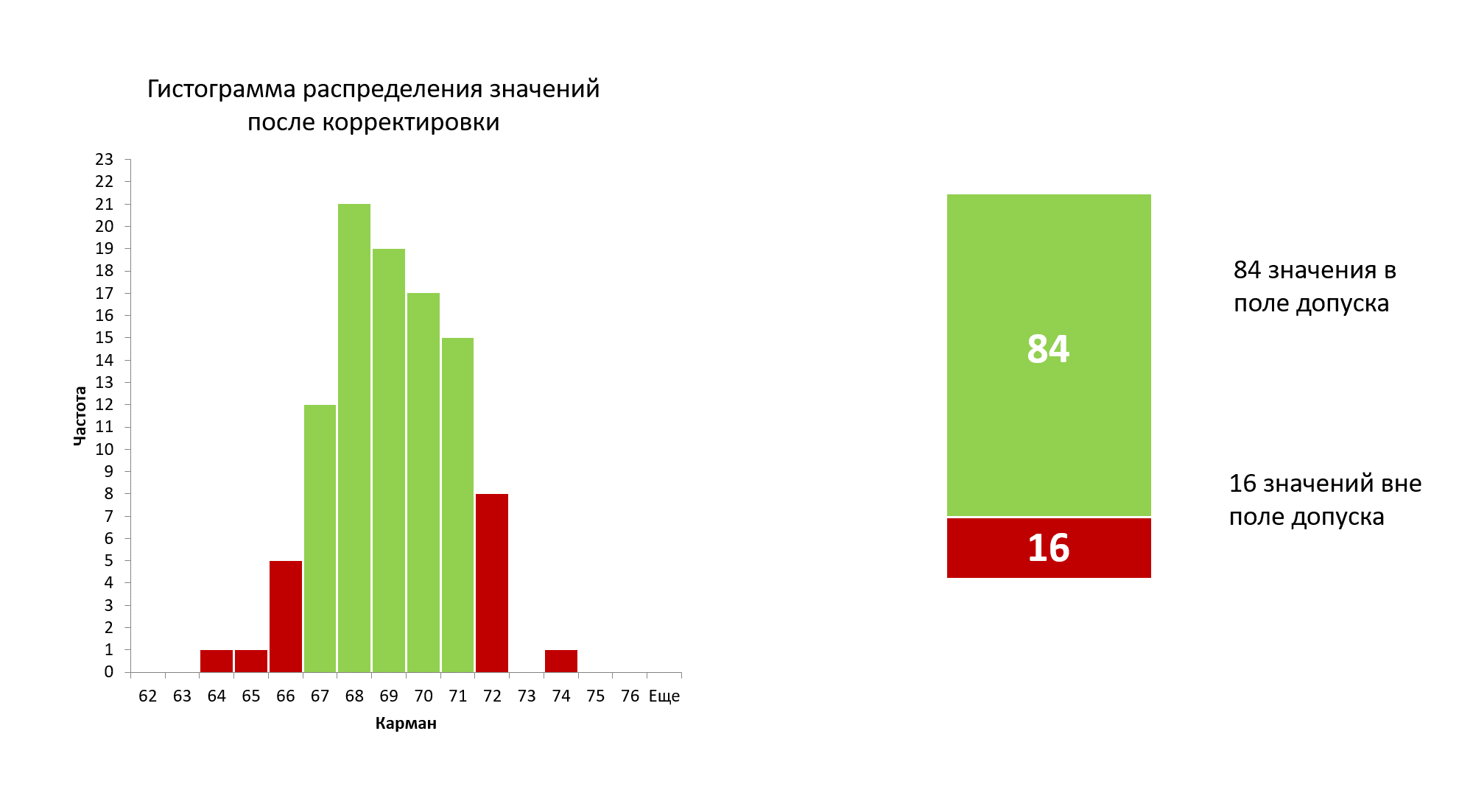
Figura 9: Histograma de la distribución de 100 nuevos valores después de eliminar las causas especiales de variabilidad previamente identificadas.
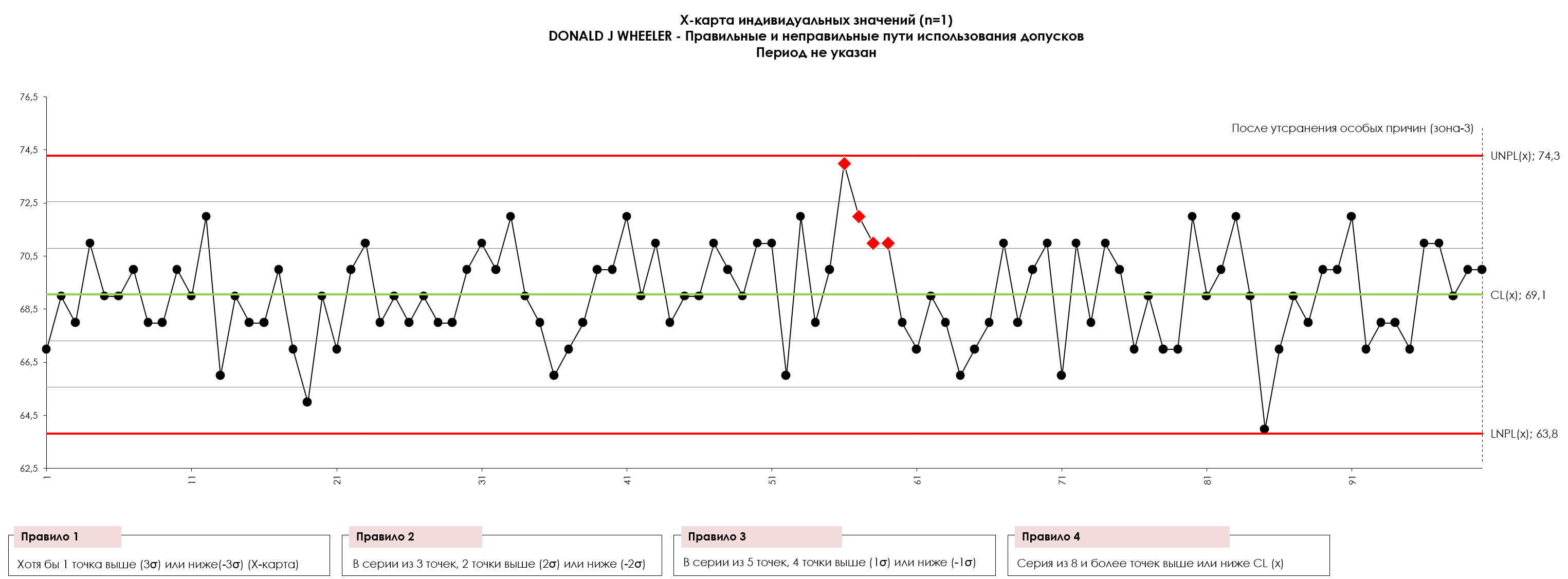
Figura 10: Mapa X de valores individuales (voz de proceso) 100 valores. El proceso de la figura funciona de forma bastante predecible. Se han eliminado causas especiales de variación previamente manifestadas, con excepción de una serie de puntos 55, 56, 57, 58, 59, 60 en los que posiblemente hayan aparecido nuevas causas especiales de variabilidad. UNPL es el límite superior de control natural del proceso, LNPL es el límite inferior de control natural del proceso, CL es la línea central (promedio). El dibujo fue preparado usando nuestro desarrollado.
“Gráficos de control de Shewhart PRO-Analyst +AI (para Windows, Mac, Linux)”
.
Nota Sergey P. Grigoryev: Puede descargar los datos del proceso estabilizados en una lista ordenada en formato CSV para crear de forma independiente un gráfico XmR de control:
descargar
.
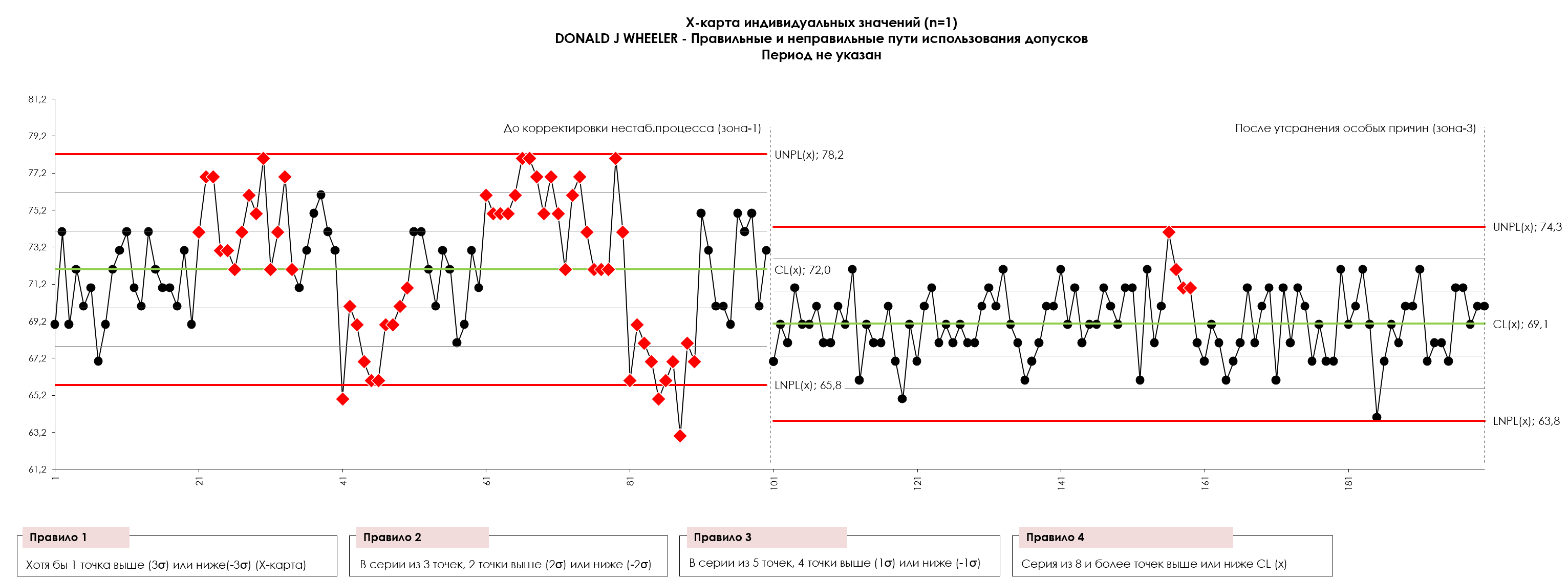
Figura 10.1: Mapa X de valores individuales (voz de proceso) de 100 valores antes de eliminar las causas especiales de variabilidad en un proceso inestable (Zona-1) y después (Zona-3). UNPL es el límite superior de control natural del proceso, LNPL es el límite inferior de control natural del proceso, CL es la línea central (promedio). El dibujo fue preparado usando nuestro desarrollado. “Gráficos de control de Shewhart PRO-Analyst +AI (para Windows, Mac, Linux)” .
Cuando empezaron a gestionar este proceso de forma predecible y según su objetivo (valor de tolerancia), su rendimiento aumentó al 84 por ciento. Este es todo el potencial de este proceso en su estado actual. Un rendimiento del 84 por ciento no es una meta imposible, sino simplemente lo que el proceso es capaz de producir cuando opera a su máximo potencial. El trabajo predictivo minimizará la variación en los resultados del proceso, mientras que el trabajo para procesar los objetivos maximizará la conformidad del producto fabricado.
Intentemos mejorar un proceso estable usando el mismo método.
Pero el proceso todavía no produce productos 100 por ciento compatibles. ¿No podemos hacer algo con respecto al 16 por ciento de productos no conformes? Bueno, ¿qué pasa si aplicamos un controlador P con una zona muerta en el campo de tolerancia de datos de la Figura 10? Cuando hacemos esto, terminamos con los datos de la Figura 11.
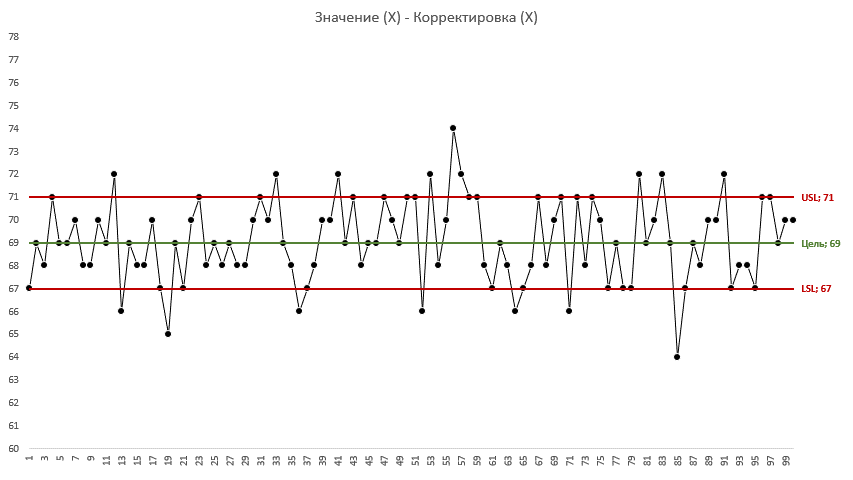
Figura 11: Se ajusta la animación del cambio de 100 valores iniciales como un proceso estable y bien centrado. USL es el límite superior de la tolerancia, Target es el valor nominal del campo de tolerancia, LSL es el límite inferior del campo de tolerancia.
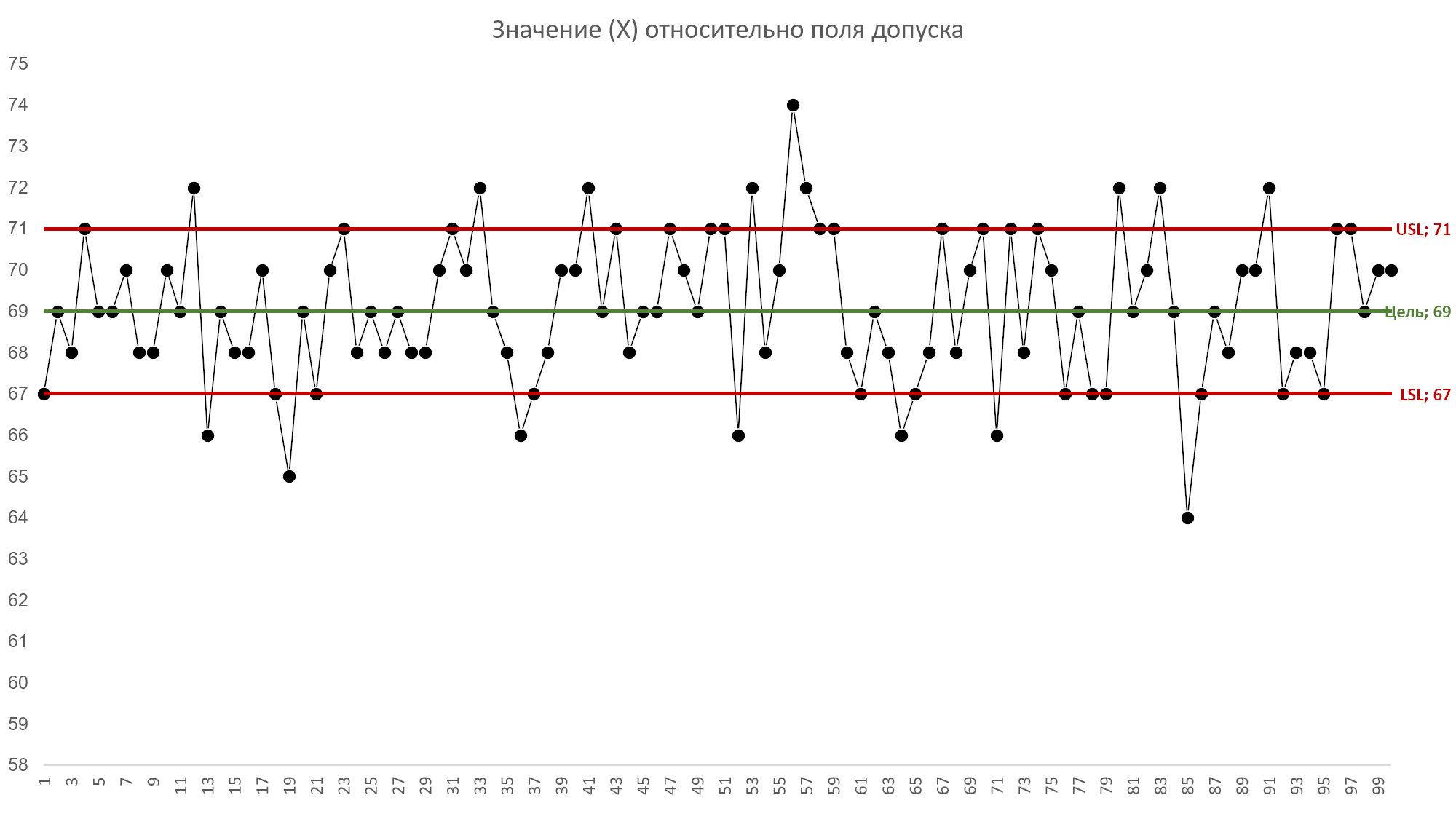
Figura 12: Gráfica de cien valores iniciales antes de ajustar un proceso estable y bien centrado contra márgenes de tolerancia (voz del cliente). USL es el límite superior de la tolerancia, Target es el valor nominal del campo de tolerancia, LSL es el límite inferior del campo de tolerancia.
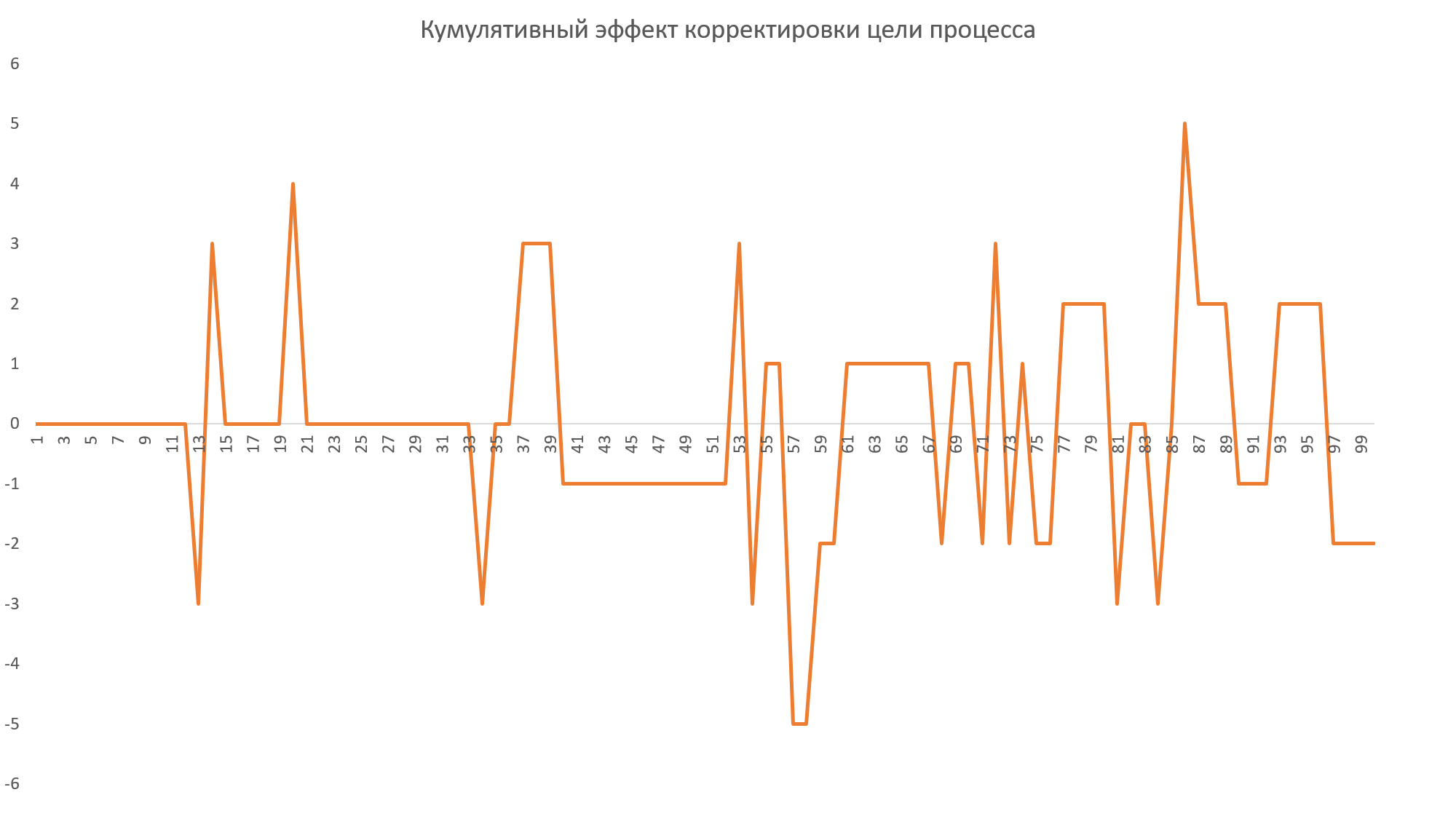
Figura 13: Efecto acumulativo del ajuste de un proceso estable y bien centrado.
Nota de Sergey P. Grigoryev: Tenga en cuenta que la gráfica del efecto acumulativo de los ajustes para un proceso estable y bien centrado presentada en la Figura 13 difiere en su simetría con respecto al eje (X) de la misma gráfica para un proceso inestable y no centrado. (Figura 6). Lo que en el caso de la Figura 13 sugiere que al intentar ajustar un proceso estable y bien centrado, simplemente estábamos jugando a mover algunos valores hacia abajo y otros hacia arriba, con lo que sólo empeoramos las cosas. "Queríamos lo mejor, pero resultó como siempre". - V.S. Chernomyrdin.
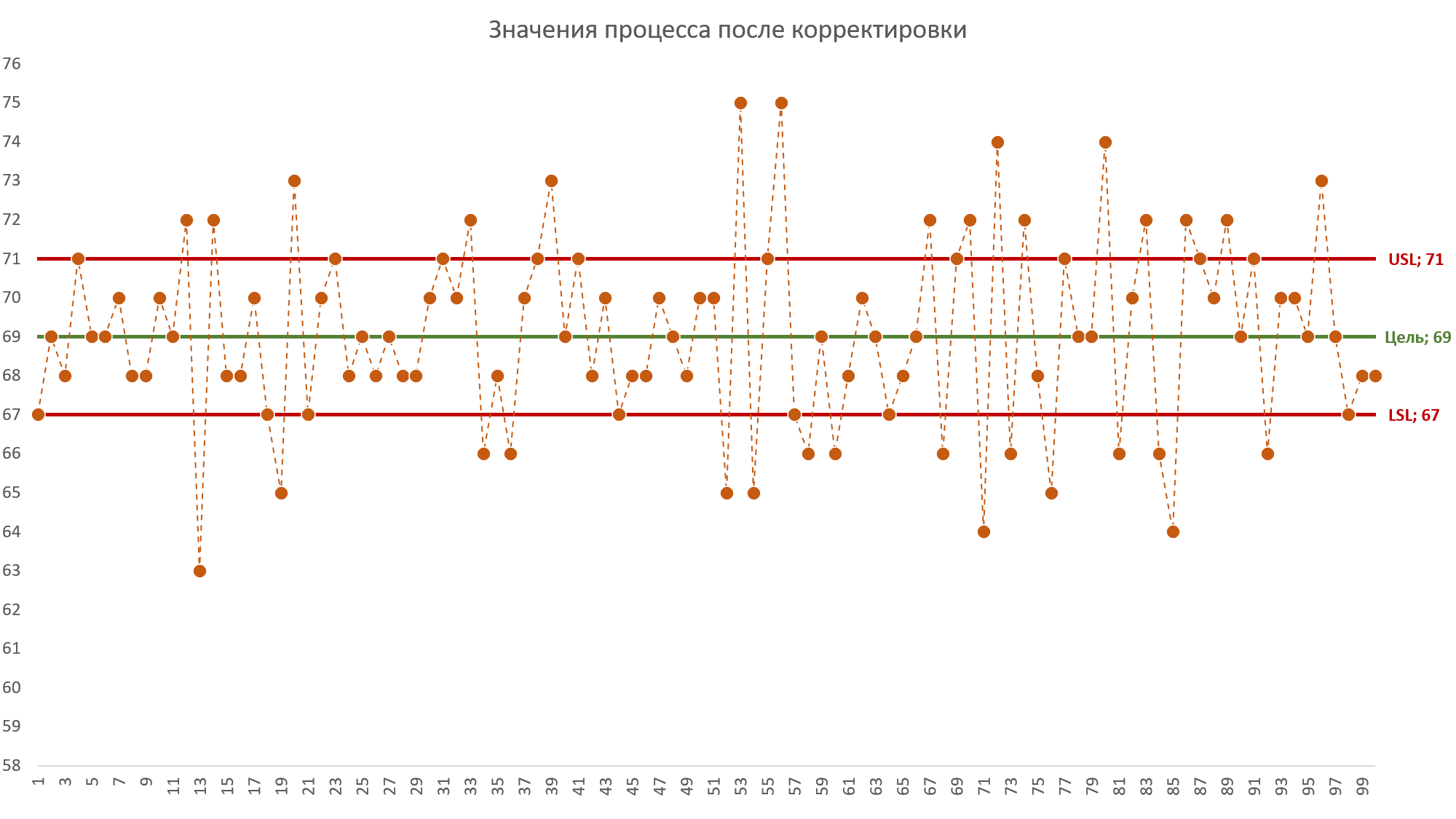
Figura 14: Datos resultantes de un proceso estable y bien centrado después de la conversión mediante un controlador P utilizando bandas de tolerancia como banda muerta. USL es el límite superior de la tolerancia, Target es el valor nominal del campo de tolerancia, LSL es el límite inferior del campo de tolerancia.
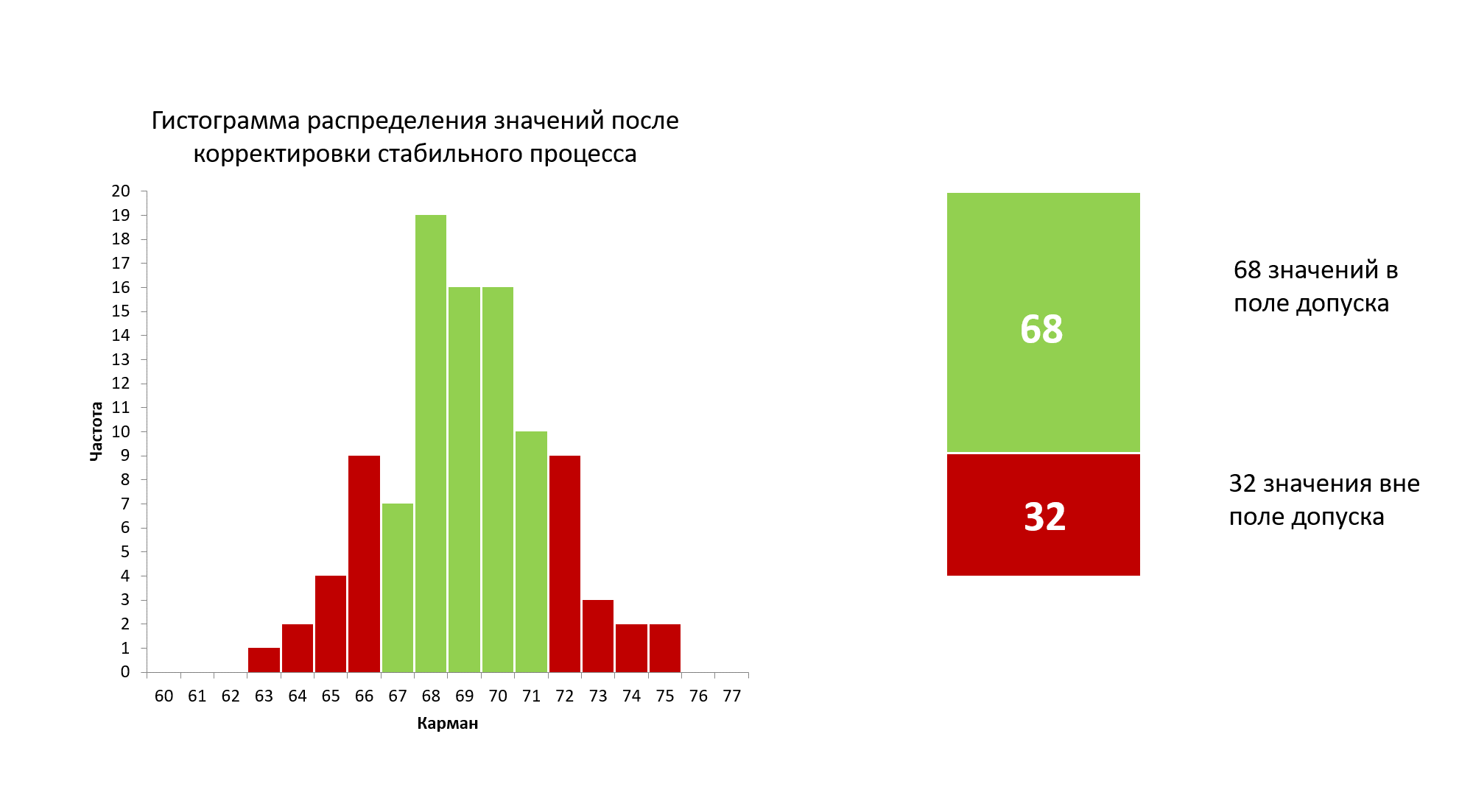
Figura 15: Histograma de la distribución de 100 nuevos valores después de intentar ajustar un proceso estable y bien centrado.
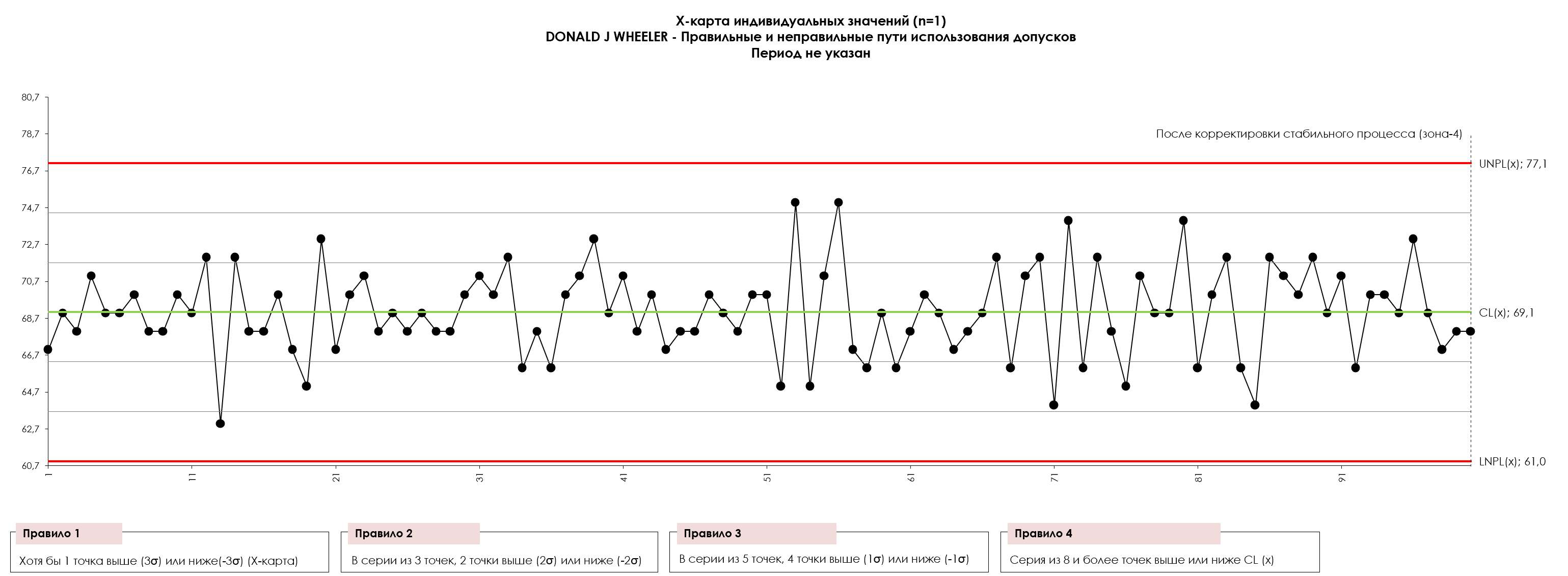
Figura 16. Mapa X de valores individuales (voz de proceso) de 100 valores después de intentar ajustar un proceso estable y bien centrado. UNPL es el límite superior de control natural del proceso, LNPL es el límite inferior de control natural del proceso, CL es la línea central (promedio). El dibujo fue preparado usando nuestro desarrollado. “Gráficos de control de Shewhart PRO-Analyst +AI (para Windows, Mac, Linux)” .
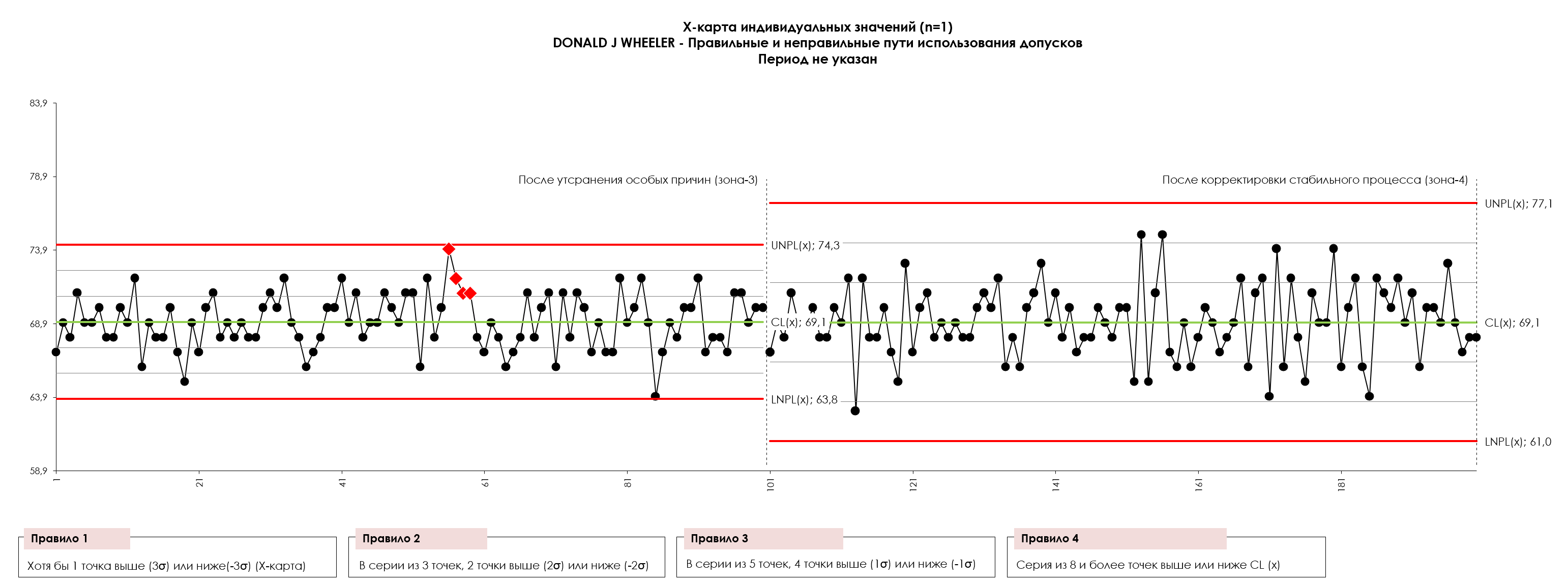
Figura 16.1. Mapa X de valores individuales (voz de proceso) 100 valores antes (Zona-3) después (Zona-4) del intento del operador de corregir un proceso estable y bien centrado. UNPL es el límite superior de control natural del proceso, LNPL es el límite inferior de control natural del proceso, CL es la línea central (promedio). El dibujo fue preparado usando nuestro desarrollado. “Gráficos de control de Shewhart PRO-Analyst +AI (para Windows, Mac, Linux)” .
Aquí el controlador P, utilizando la banda de tolerancia como banda muerta, convirtió un proceso que tenía un 84% de cumplimiento en otro proceso con un 68% de cumplimiento. La proporción de productos no conformes se duplicó del 16 al 32 por ciento.
¿Por qué pasó esto? Esto se debió a que el controlador P reaccionó al ruido y realizó ajustes inadecuados. Con sólo unos pocos ajustes en el primer caso (Figura 2), el controlador P comenzó a producir resultados positivos, pero finalmente los ajustes innecesarios alejaron el proceso de la meta y empeoraron la situación.
Nota de Sergey P. Grigoryev: Para intentar mejorar un proceso estable, fue necesario hacer 32 ajustes. El tiempo perdido para los ajustes no hizo más que empeorar la situación con las mismas acciones que en el primer caso (Figura 2). Esto puede dejar a cualquier operador altamente capacitado en un estupor total. ¿Qué crees que hará el operador en este caso? ¿La gerencia lo ayudará a resolver este problema? ¡Oh, si tan sólo la dirección pudiera saber esto! El resultado de cualquier intento de corregir un proceso estable y bien centrado se explica en un lenguaje sencillo en el experimento. con embudo y objetivo Eduardo Deming.
"Nosotros mismos destruiremos todo con nuestros propios esfuerzos persistentes".
En la Figura 2, el proceso no estaba centrado en el campo de tolerancia y se comportaba de forma impredecible. Allí, el controlador P, utilizando la banda de tolerancia como banda muerta, realmente mejoró las cosas. En la Figura 14, este proceso estaba centrado y era predecible. Allí, el controlador P simplemente añadió ruido al proceso, lo que aumentó la variación en el flujo del producto y empeoró las cosas.
Entonces, ¿a qué conclusión hemos llegado? ¿Podemos utilizar la tolerancia para regular un proceso que se encuentra en un estado estadísticamente incontrolable? Si bien usar un controlador P usando la banda de tolerancia como banda muerta puede ser mejor que no hacer nada, no le permite aprovechar al máximo su proceso.
¿Por qué el controlador P es ineficaz cuando el proceso opera de manera predecible y está centrado dentro del rango de tolerancia? Cualquier mecanismo de control de procesos manual y automatizado es inherentemente reactivo. Ya sea un controlador P simple o un controlador PID más complejo, no pueden actuar hasta que reciben una señal detectada. Debido a que el proceso original era impredecible y no estaba centrado dentro de la tolerancia, hubo muchas señales reales que el controlador P captó. Sin embargo, también hubo algunas señales débiles (ruido) a las que respondió el controlador P, lo que resultó en ajustes innecesarios. Si la zona muerta está completamente desafinada con la voz del proceso, su mecanismo de ajuste del proceso dará como resultado demasiados ajustes. En cualquier caso, el resultado será una mayor variabilidad en el flujo del producto. El uso de un controlador automático para un proceso estable generalmente resulta en una mayor variabilidad de la que el proceso es capaz de hacer cuando está operando a su máximo potencial.
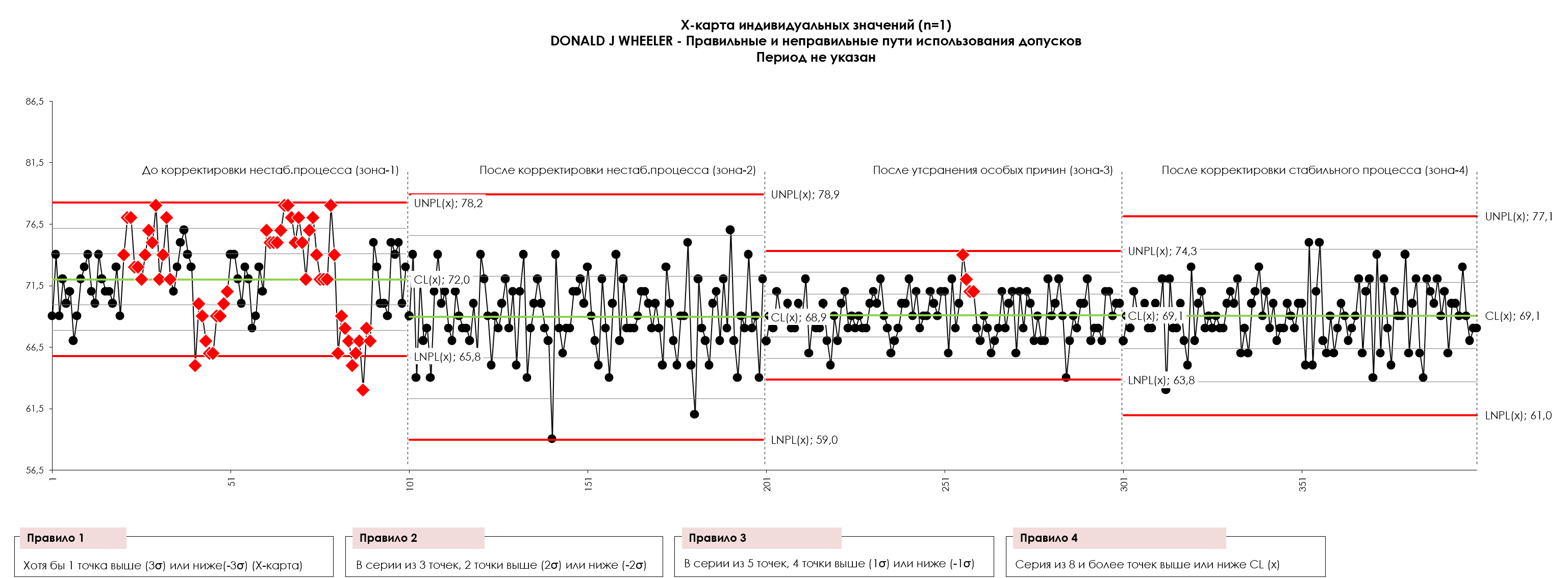
Figuras 2; 8.1; 10; 16. Mapa X de valores individuales (voz de proceso) 100 valores para todos los casos analizados en el artículo anterior. UNPL es el límite superior de control natural del proceso, LNPL es el límite inferior de control natural del proceso, CL es la línea central (promedio). El dibujo fue preparado usando nuestro desarrollado. “Gráficos de control de Shewhart PRO-Analyst +AI (para Windows, Mac, Linux)” .
Vea un ejemplo de intervención del operador en el proceso de control del flujo de gas en una empresa que produce metano biogénico en el artículo: El concepto de variabilidad en el control de procesos. .
Error del primer tipo
- "¡Pero eso significa que no reaccionarás ante valores que estén fuera de especificación!"
Sí, los valores no conformes de 64, 65, 66 y 72, 73, 74 son parte de lo que produce este proceso cuando se ejecuta de manera predecible y bien centrado dentro de la tolerancia. Déjame repetir. Como puede ver en las Figuras 9 y 10, cuando este proceso esté funcionando a su máximo potencial, producirá un producto en el rango de 64 a 74 (eje Y). Tomados uno a la vez, estos valores no son una señal de que haya algún problema con el proceso, aunque puedan estar fuera de las especificaciones. Los campos de tolerancia están diseñados para separar los productos adecuados de los inadecuados. Son la voz del cliente, no el proceso. Los campos de autorización nunca deben confundirse con la voz del proceso en sí.
- “¿Estás diciendo que debería ignorar los productos no conformes?”
El producto no conforme debe ser rechazado. Pero si su proceso se controla de manera predecible y se ajusta al objetivo, el hecho de que un elemento no cumpla no le indica que se requiere un ajuste del proceso.
Nota de Sergey P. Grigoryev: En este caso, futuras mejoras requerirán cambios sistémicos (cambio de materias primas, tecnología, equipos, herramientas, capacitación de operadores, etc.).
Por supuesto, el control de procesos no se puede controlar de manera predecible y centralizada sin trazar un diagrama de comportamiento del proceso (gráfico Shewhart XmR de valores individuales), por lo que no debería haber conjeturas. Si no tiene un diagrama de comportamiento del proceso, las posibilidades de que esté ejecutando su proceso de manera impredecible son al menos de 10 a 1. Si este es el caso, entonces un controlador de proceso automático sólo le permitirá lograr una fracción de lo que su proceso es capaz de hacer.
Breve información
El movimiento moderno por la calidad trata de aprender a dejar de quemar tostadas. Esto no quiere decir que no tengamos que pelar las tostadas de vez en cuando; Esto significa que avanzamos hacia arriba para trabajar en el proceso en lugar de separar el material bueno del malo al final de la línea de producción. Los campos de tolerancia siguen siendo relevantes, todavía definen la voz del cliente, pero es importante distinguirlos de la voz del proceso. Si bien queremos que la voz del proceso esté alineada con los campos de tolerancia (voz del cliente), los campos de tolerancia no brindan la información correcta sobre lo que se debe hacer para aprovechar todo el potencial de su proceso.
Otro caso sencillo (Sergey P. Grigoryev)
Estoy seguro de que es necesario considerar una situación más cuando el proceso se encuentra en un estado estadísticamente estable (controlado), pero no está centrado en el campo de tolerancia. En un ejemplo de este tipo de proceso, 77 valores están fuera del rango de tolerancia.
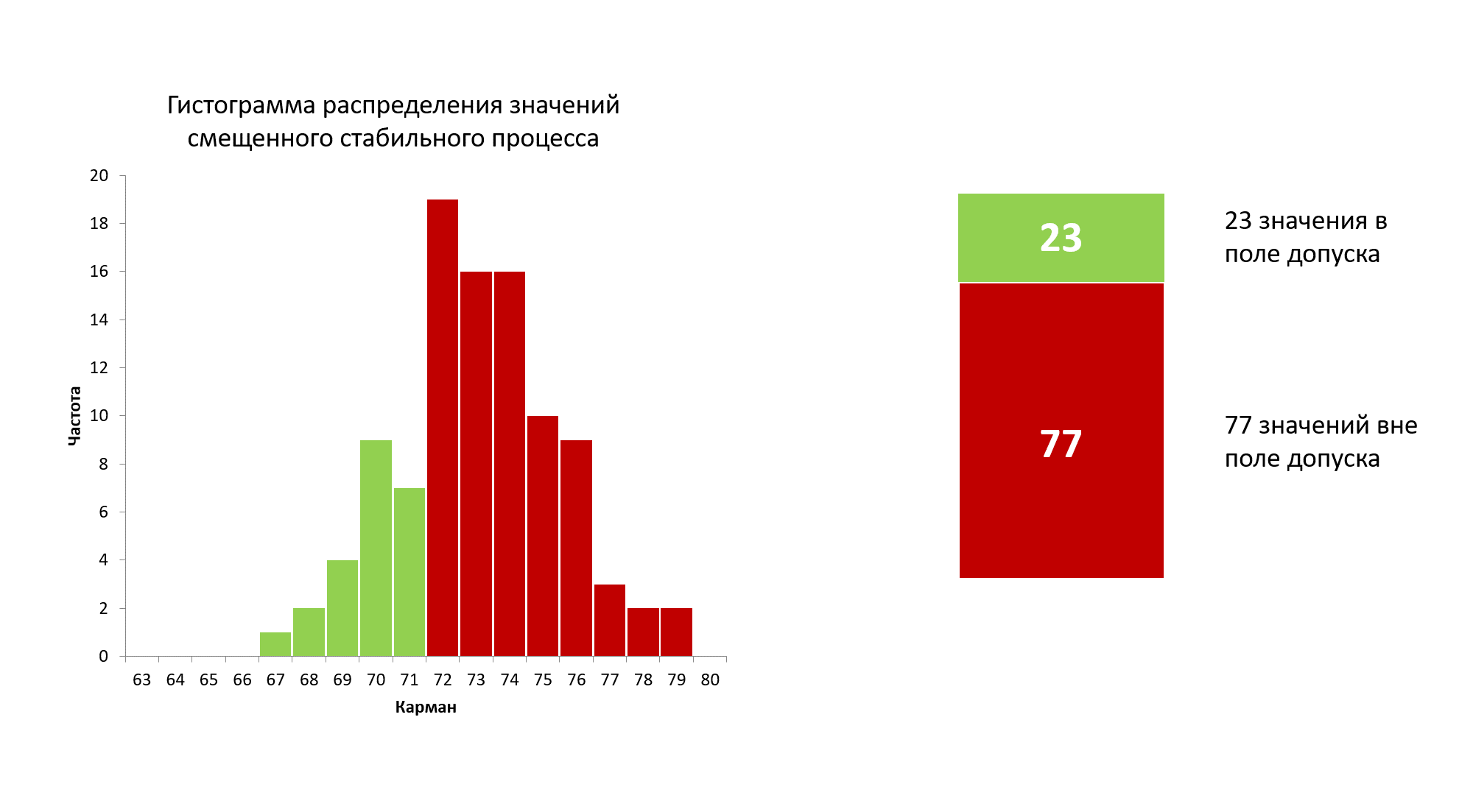
Figura 17: Histograma de la distribución de 100 valores iniciales de un proceso estable pero mal centrado.
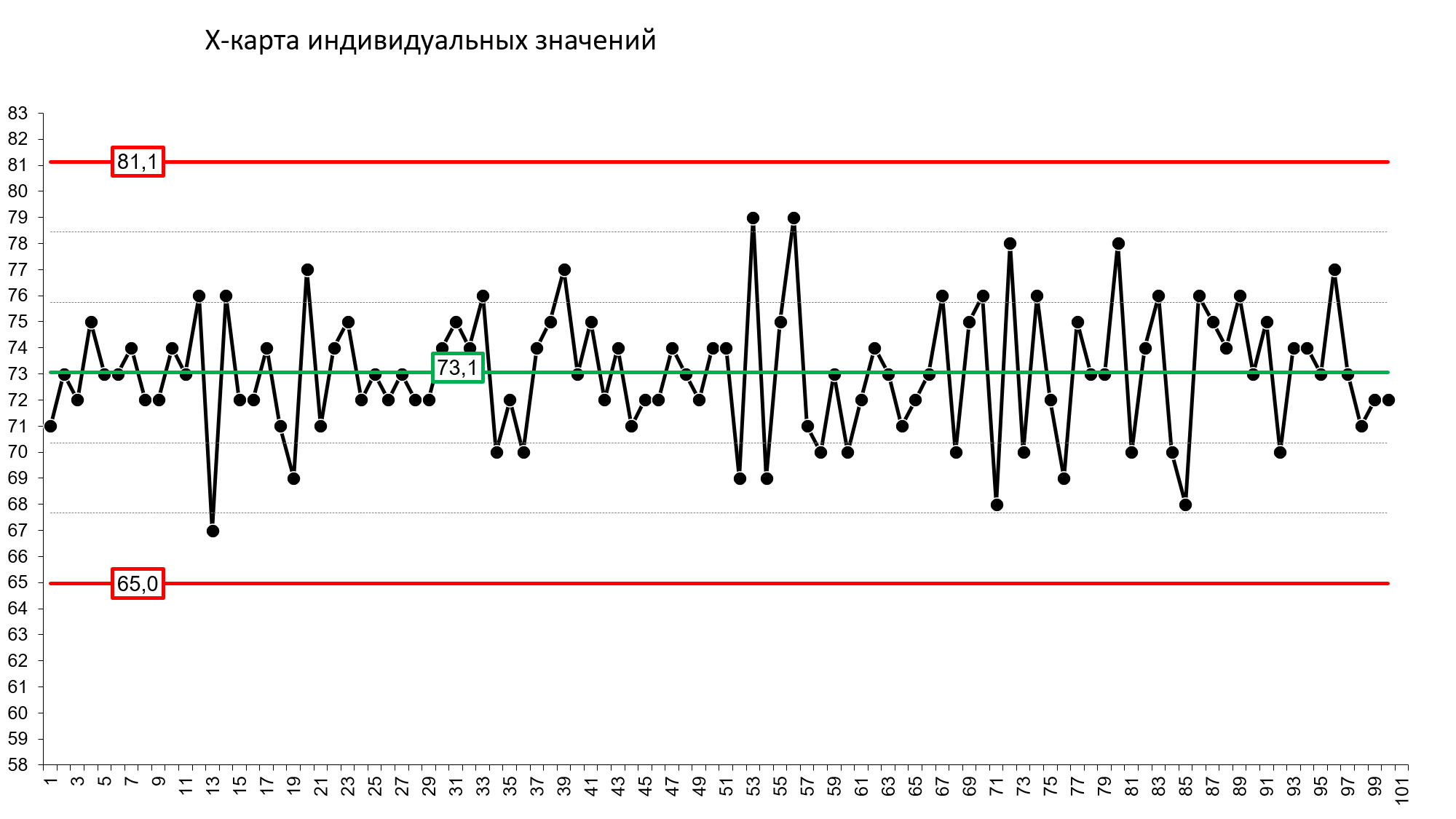
Figura 18. Mapa X de valores individuales (voz de proceso) de 100 valores iniciales de un proceso estable pero mal centrado. Las líneas rojas, respectivamente, son los límites naturales superior e inferior del proceso, la línea verde es la línea central (promedio) del proceso.
En este caso, sólo será necesario un ajuste para centrar el proceso dentro del rango de tolerancia. Simplemente cambie la configuración de la máquina una vez para compensar el proceso estable promedio desde el centro de la zona de tolerancia.
Entonces, si el promedio de un proceso estable y mal centrado es 73,1 y el centro del campo de tolerancia es 69. El desplazamiento de un proceso estable y mal centrado: 69,0-73,1 = -4,1
Es por la cantidad de desplazamiento que se deben cambiar los ajustes de la máquina que produce estas piezas. Y llamar al servicio técnico, que deberá configurar la máquina. Vea el resultado a continuación.
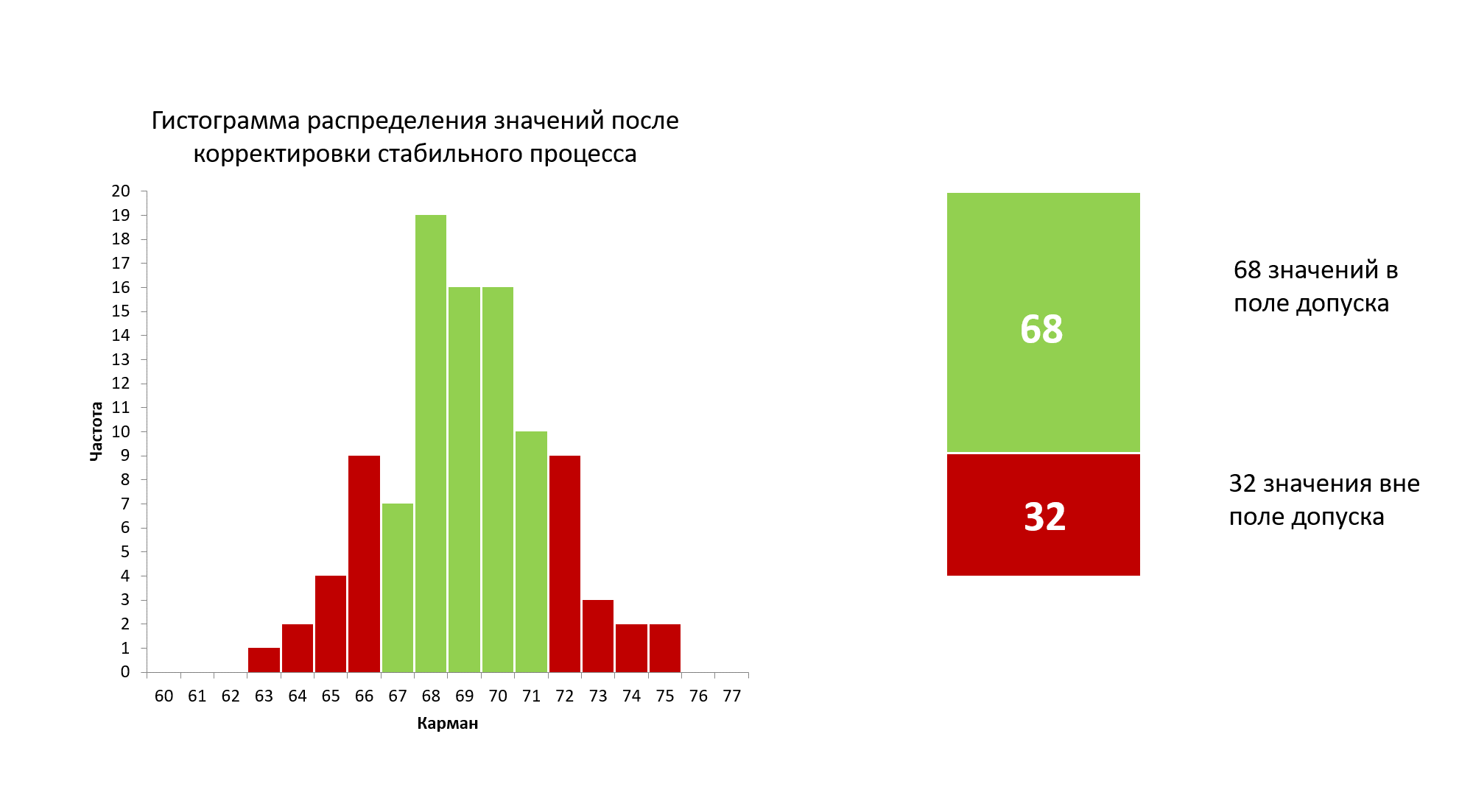
Figura 19: Histograma de la distribución de 100 nuevos valores después de centrar en el campo de tolerancia de un proceso estable.
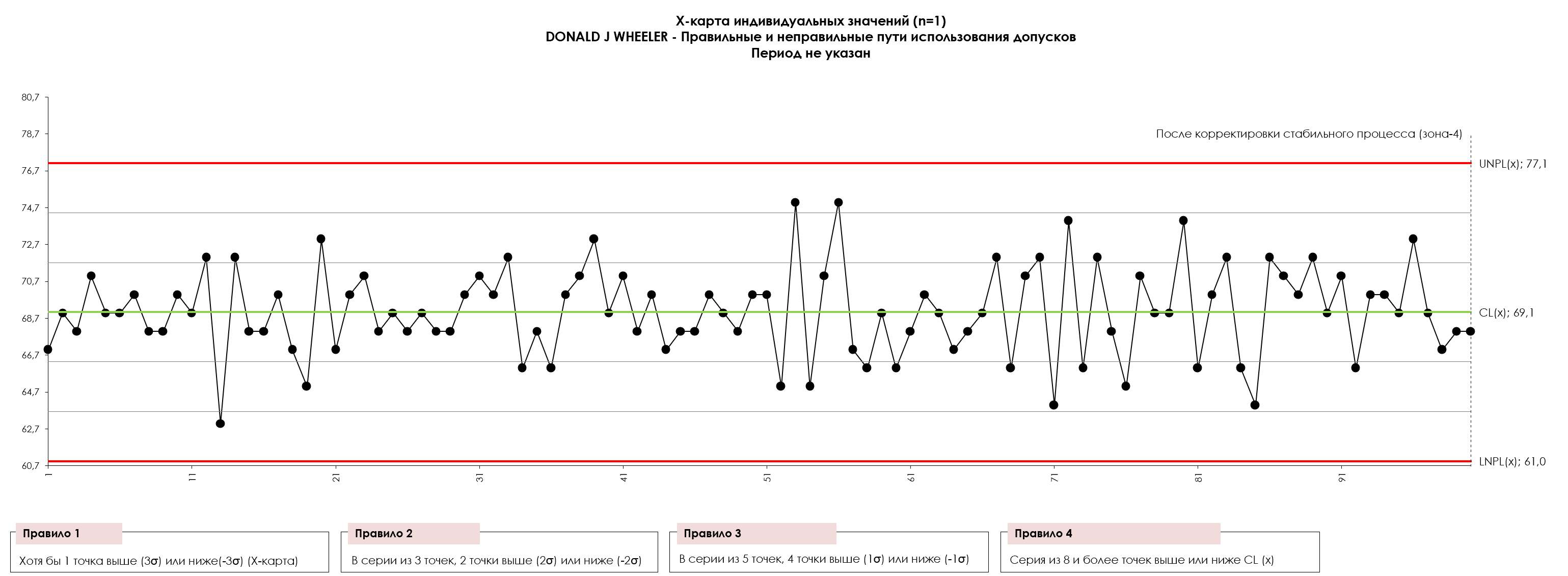
Figura 20. Mapa X de valores individuales (voz de proceso) 100 valores nuevos después de centrar en el campo de tolerancia del proceso estable. Las líneas rojas, respectivamente, son los límites naturales superior e inferior del proceso, la línea verde es la línea central (promedio) del proceso. El dibujo fue preparado usando nuestro desarrollado. “Gráficos de control de Shewhart PRO-Analyst +AI (para Windows, Mac, Linux)” .
Si cree que este último caso es poco común, está muy equivocado. Si no mantiene gráficos de control de sus procesos y construye histogramas de la distribución de indicadores en relación con los campos de tolerancia, ni siquiera podrá juzgar esto. Si está familiarizado con los índices de rendimiento (reproducibilidad) del proceso Cp (índice de espacio habitable) y Cpk (índice de centrado del proceso), entonces debe saber que Cpk en la gran mayoría de los casos es menor que Cp, lo que indica un cambio en el promedio. proceso desde el centro del campo de tolerancia hacia el límite de tolerancia inferior o superior. En cualquier caso, centrar tanto los procesos estables como los inestables en la zona de tolerancia reduce la proporción de piezas defectuosas del proceso que superan los límites de tolerancia en "un clic". En los casos en que el proceso opera dentro de la zona de tolerancia, el centrado mejora significativamente la calidad de las piezas y conjuntos (DSE), acercando la mayoría de las piezas al centro de la zona de tolerancia (para zonas de tolerancia simétricas). La última declaración explica Función de pérdida de Taguchi .
Mejoras en el proceso de 77 piezas defectuosas a 32 con un ajuste.
"¿Qué te parece eso, Elon Musk?"
¡Importante!
- La única forma económicamente factible de mejorar significativamente la calidad es primero llevar el proceso a un estado controlado estadísticamente y solo después comenzar a centrarlo en la zona de tolerancia.
- Antes de cualquier investigación de proceso, asegúrese de que su sistema de medida , que es utilizado por el operador que realiza ajustes al proceso tecnológico, está en un estado estadísticamente controlado, no tiene un sesgo significativo, averigüe si su precisión es suficiente para evaluar el proceso, si las mediciones uniformes son adecuadas (profundidad de medición) o, por el contrario, si estás grabando ruido. - Ver descripción de nuestro software Gráficos de control de Shewhart .
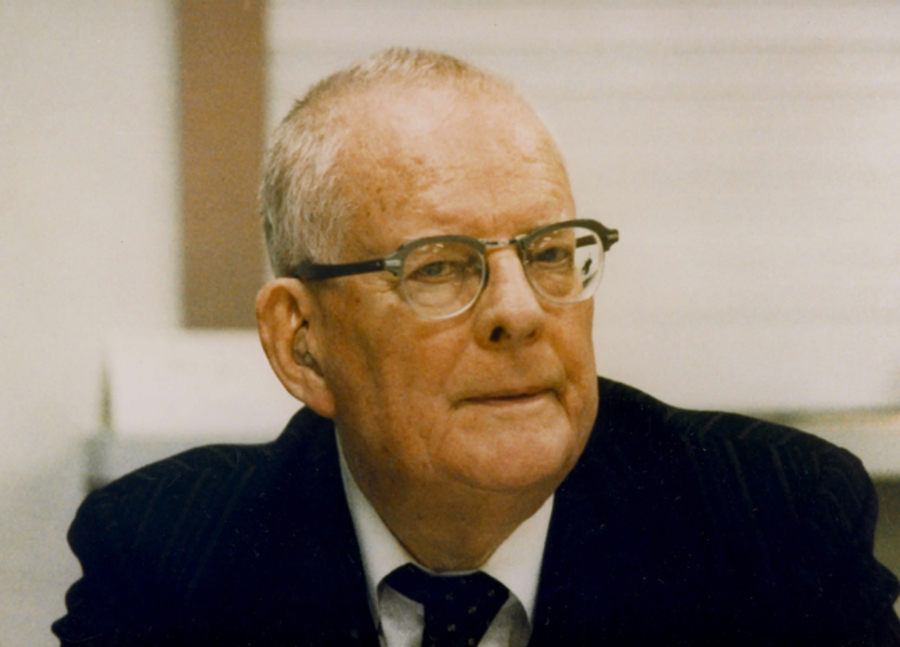
"No hay sustituto para el conocimiento. Pero la perspectiva de utilizar el conocimiento es aterradora".