Sin integrar métodos de control estadístico en sistemas automatizados de control de procesos, sistemas de control automatizados y sistemas de gestión de datos, sistemas de control automatizados, sistemas de control automatizados, aumentará la cantidad de errores del primer y segundo tipo cometidos al controlar los procesos tecnológicos.
Material elaborado por: Director Científico del Centro AQT Serguéi P. Grigoriev .
El libre acceso a los artículos no disminuye en modo alguno el valor de los materiales contenidos en ellos.
Los operadores de sistemas automatizados de control de procesos o reguladores automáticos, al intentar controlar los procesos, cometen constantemente errores del primer y segundo tipo, sin entender cómo distinguir el ruido de una señal, lo que reduce la eficiencia económica de los procesos controlados y aumenta la probabilidad de incidentes de emergencia. .
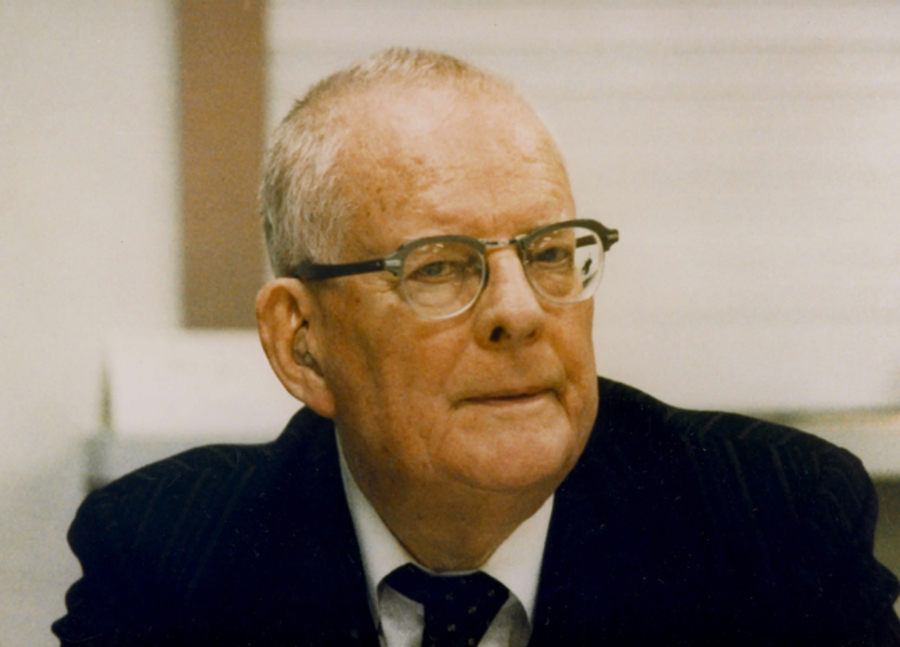
"No hay sustituto para el conocimiento. Pero la perspectiva de utilizar el conocimiento es aterradora".
Los productos de software de sistemas de control de procesos y sistemas de control automatizados de empresas como Siemens, GE, etc. ya utilizan módulos de control de procesos estadísticos integrados (que separan la variabilidad natural del proceso y la variabilidad no natural causada por razones especiales), cuya herramienta principal son los gráficos de control de Shewhart. Pero estas empresas tampoco supieron darse cuenta de las principales ventajas de los métodos estadísticos para el control de procesos previos, utilizándolos únicamente en módulos de control de calidad para los procesos de producción multifactoriales resultantes.
Cualquier indicador agregado (resultante) oculta las señales de variabilidad en las fuentes de datos, convirtiéndolas en ruido en el nivel resultante, privando así al personal de la capacidad de ver qué se debe hacer para mejorar los procesos en primer lugar. Al mismo tiempo, cualquier reacción del operador del sistema automatizado de control de procesos o de los controladores automáticos al ruido es un error del primer tipo, que sólo empeora la situación. Es importante comprender que con un alto nivel de agregación, solo se notarán cambios catastróficos en forma de señales (Edwards Deming).
"La búsqueda ascendente es una palanca poderosa para resolver problemas de mezclas".
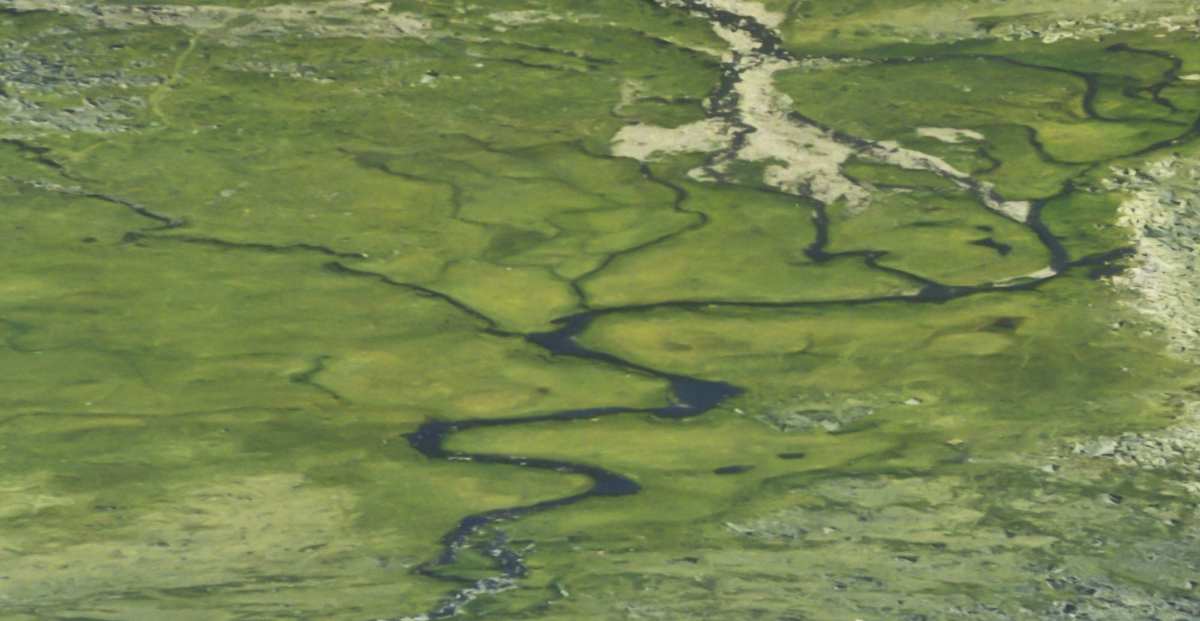
Figura 1. La búsqueda ascendente es una palanca poderosa para resolver problemas de mezclas.
Un asistente del sistema para encontrar y eliminar razones especiales por las que los procesos tecnológicos están fuera de control (fuera de un estado controlado estadísticamente) debe ser una visualización visual de los gráficos de control en la interfaz del operador para todos los elementos identificados de la relación causa-efecto. Además, el estado de control estadístico de los indicadores de causas (factores) monitoreados se puede evaluar tanto a partir de datos provenientes de sensores como de datos de otros subsistemas que registran eventos en línea (por ejemplo, control de calidad entrante de materias primas, datos de un laboratorio de pruebas). y control interoperacional).
Además, los métodos de control estadístico permiten identificar la presencia de factores (causas generales y especiales de variabilidad) que no son monitoreados por sus sistemas de control de procesos, pero que influyen significativamente en la cantidad de variabilidad y estabilidad de los procesos tecnológicos. Dichos factores deben definirse operativamente y se les deben asignar métricas para su control en el sistema de control de procesos.
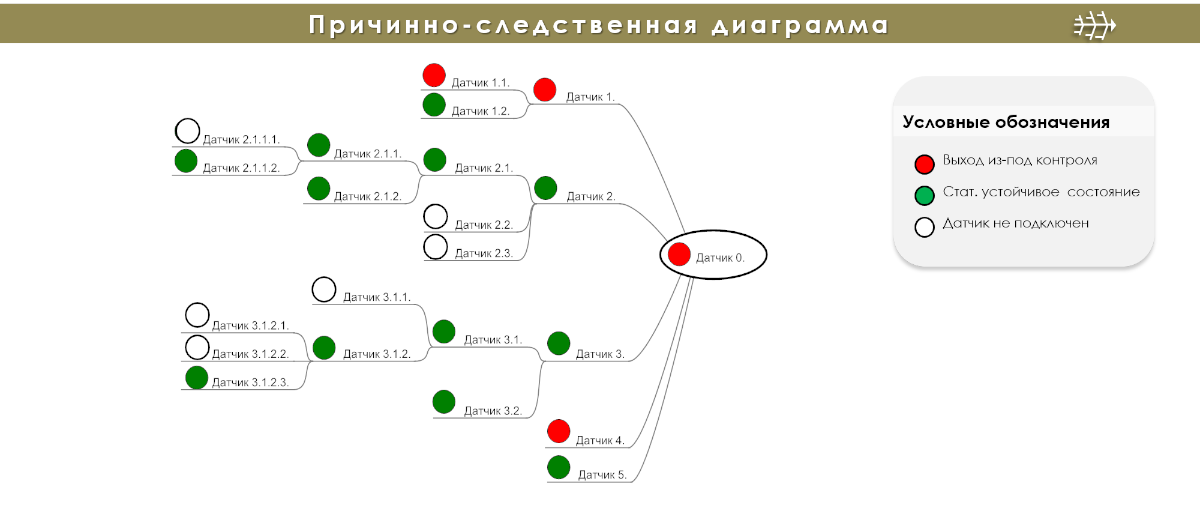
Figura 2. Relación causa-efecto de los datos resultantes de los sensores del sistema de control automatizado de procesos. Los puntos que indican la salida del proceso de un estado estadísticamente estable se muestran en rojo, independientemente del grado en que se alcancen los límites de advertencia o emergencia.
La gran mayoría de los sistemas de control automatizados para procesos tecnológicos y redes de servicios públicos (APCS, ASUB, SMUS, ASUiD, Process Control System) utilizados en la industria no están equipados con software y módulos analíticos para el control estadístico de procesos (Statistical Process Control, SPC), y El personal del operador no está capacitado en estas técnicas de manejo.
Esto lleva al hecho de que los operadores, en un intento de gestionar los procesos, hacen constantemente errores de primer y segundo tipo , sin entender cómo distinguir la variabilidad natural de un proceso estadísticamente controlado (ruido) de lo no natural (señal), este último es causado por el proceso que se sale de control bajo la influencia de razones especiales.
Si se aplican correctamente, los gráficos de control de Shewhart separan operativamente con precisión el ruido de las señales, revelando la firma individual de los equipos y las fallas del proceso sin requerir que se establezcan valores límite ficticios. Por ejemplo, OSyS (Optimized Systems and Solutions, una filial de Rolls-Royce), que se especializa en proporcionar DSS para monitorear y optimizar activos de alto valor, informó sobre un problema que indica una falta de dicho conocimiento:
"Al analizar los parámetros de rendimiento, los especialistas de OSyS se enfrentaron al hecho de que o tenían que establecer valores de umbral demasiado estrechos y luego el número de alertas aumentaría drásticamente, o los valores eran demasiado amplios. y luego resultó que los valores en la alerta no cumplían con los límites requeridos. Sin embargo, las herramientas técnicas, el conocimiento y las habilidades de análisis les ayudaron a crear una firma de falla para todo tipo de flujos de datos que pueden provenir del equipo. "
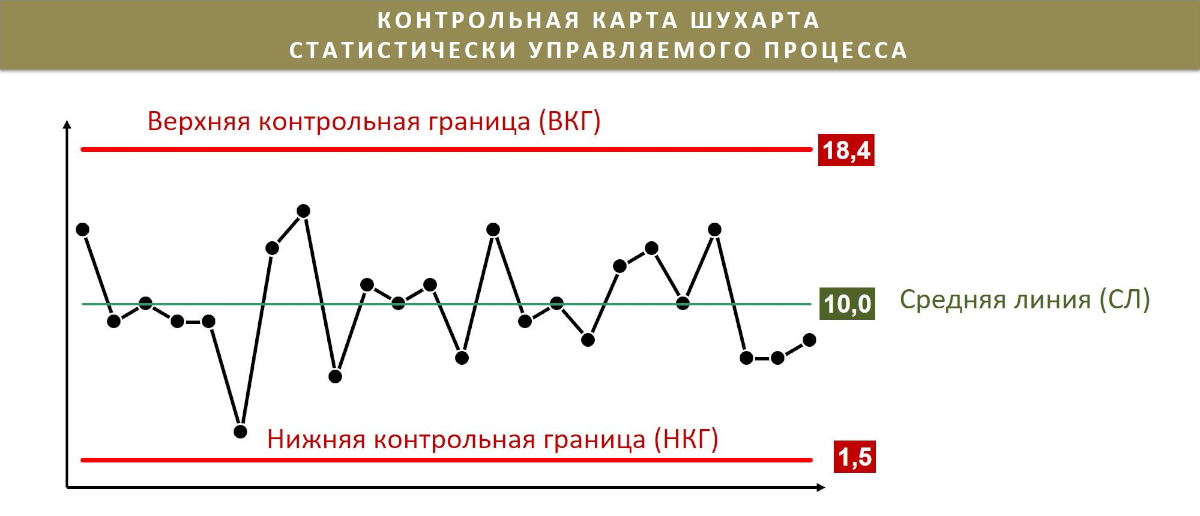
Figura 3. ВКГ y НКГ: límites de control superior e inferior obtenidos mediante cálculo a partir del análisis de datos históricos del proceso analizado con su variabilidad inherente. Literatura: Para conocer las reglas para la construcción de gráficos de control de Shewhart, consulte GOST R 50779.42-99 (ISO 8258-91) - [11.1] Métodos estadísticos. Gráficos de control de Shewhart.
Un error del primer tipo (sobrerregulación), ver Figura 4, se manifiesta en forma de intervención manual o automática constante en un proceso que se encuentra en un estado estadísticamente controlado, regulándolo de acuerdo con las reglas: 2, 3 y 4. experimentos con un embudo, cuando alcanza los límites de emergencia (límites para el inicio de la regulación, valores límite). Básicamente, responde al ruido de los datos como si fuera una señal. Los puntos dentro de los límites de una carta de control de Shewhart son homogéneos y no difieren entre sí, a pesar de la aparente diferencia en el significado de estos datos, a menos que estos puntos se extiendan más allá de los límites de control o formen estructuras que indiquen la presencia de causas especiales de variación. Las reglas para definir tales estructuras en los datos a menudo se denominan Criterios zonales de Western Electric .
La intervención reactiva en un proceso que se encuentra en un estado estadísticamente controlado (que no muestra evidencia de causas especiales de variabilidad) al regularlo conduce a una variabilidad aún mayor (dispersión de los datos de salida alrededor del valor promedio) si el espacio vital del proceso lo permite o a una distribución de datos casi uniforme dentro de los límites de la respuesta automática, si el espacio vital del proceso está limitado por estos límites, lo que oculta al observador la naturaleza natural del proceso, lo que significa que las posibilidades de mejorar dichos procesos se reducen significativamente.
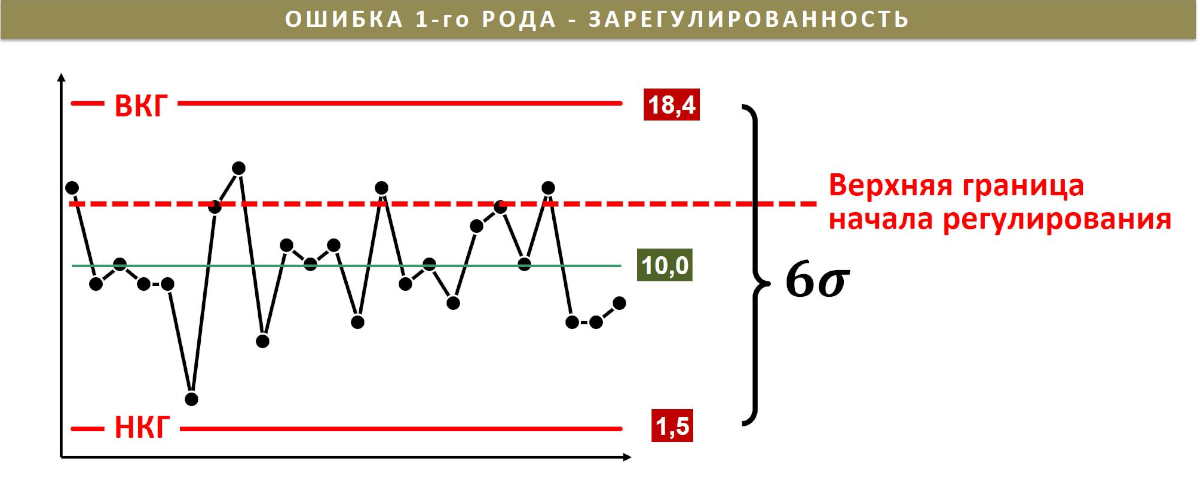
Figura 4. Error del primer tipo: sobrerregulación. El límite para el inicio de la regulación por parte del operador o automatización se ubica dentro de los límites de control del proceso.
Un error del segundo tipo, ver Figura 5, consiste en la inacción de los operadores (control insuficiente de los procesos en curso), cuando el proceso sale del estado de controlabilidad estadística (se vuelve impredecible), pero aún no ha cruzado los límites máximos de tolerancia establecidos para eso límites de emergencia (límites de inicio de regulación, cantidades límite). Un error del segundo tipo sería cualquier razonamiento sobre las capacidades potenciales de un proceso que se encuentra en un estado estadísticamente incontrolable.
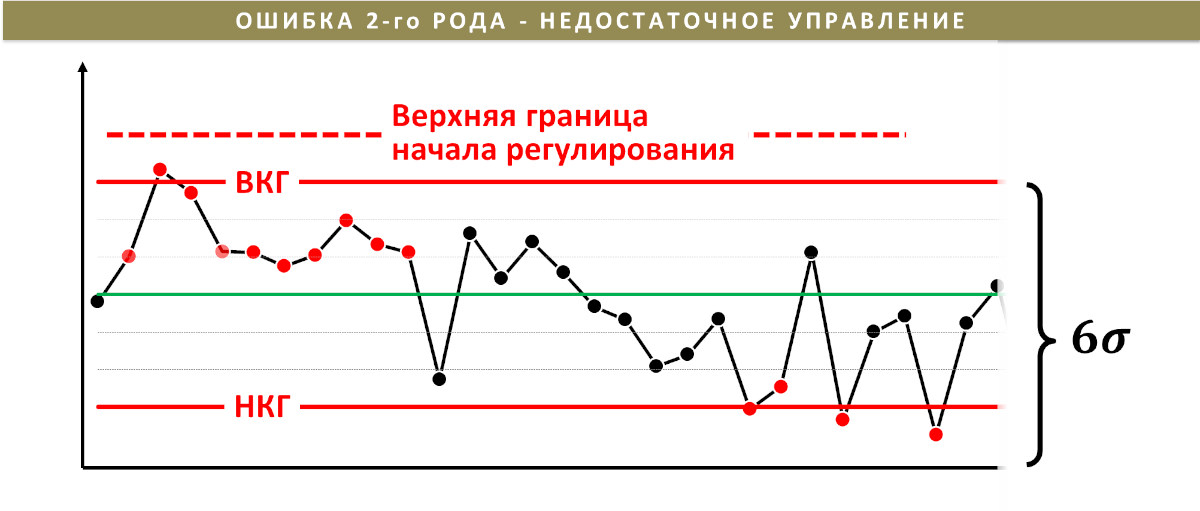
Figura 5. Error del segundo tipo: control insuficiente (inacción). El límite para el inicio de la regulación por parte del operador o automatización se ubica fuera (arriba o debajo) de los límites de control del proceso. El proceso está fuera de control, pero nadie reacciona.
Aplicación del control automático clásico en sistemas de control de procesos automatizados, controladores PID ( Controlador proporcional-integral-derivativo ), ignora el conocimiento sobre la variabilidad de cualquier proceso tecnológico y no resuelve el problema de los errores de primer y segundo tipo. El uso de tales reguladores automáticos o control de procesos manual solo puede ser efectivo para procesos que se encuentran en un estado estadísticamente incontrolable, ver Figura 5. Pero lo más probable es que, debido a un segundo tipo de error introducido por los diseñadores del sistema de control de procesos automatizado y el Debido a la falta de conocimiento necesario entre los tecnólogos, la regulación necesaria no se aplicará hasta que este proceso alcance los límites de la regulación.
No saber cómo minimizar el riesgo de cometer errores del primer y segundo tipo conlleva pérdidas y, en ocasiones, graves consecuencias.
En el artículo se describe un error más práctico del primer tipo: El concepto de variabilidad y control de procesos. , autores Netsvetaev A. G., Rubanik Yu. T., Mikhalchenko V.V.
Hoy en día, los sensores de un sistema de control de procesos automatizado son capaces de recopilar datos a una frecuencia de 20.000 Hertz. ¿Con qué frecuencia se deben recopilar datos para que los gráficos de control de Shewhart a partir de dichos datos representen adecuadamente la variabilidad del proceso? Vea el artículo de Donald Wheeler: "Frecuencia efectiva de adquisición de datos para gráficos de control de Shewhart".
Para el diagnóstico operativo (análisis de controlabilidad estadística, previsibilidad) de un proceso y tomar las medidas necesarias para ello, evitando errores del primer y segundo tipo, se pueden utilizar datos de "voz" de cualquier proceso tecnológico, recopilados de forma automática o manual:
- cualquier indicador clave de desempeño, eficiencia de adquisiciones, ventas, diseño, mantenimiento de equipos, etc.;
- datos sobre control de C&M entrantes, gestión de calidad de proveedores, calidad de productos semiacabados y productos propios;
- frecuencia de eventos (incidentes, incidentes), posibles datos de conteo (defectos, averías, paradas no planificadas, etc.);
- datos sobre tamaño, peso, holgura, caudal, nivel de líquido, vibración (diagnóstico de vibración), presión, temperatura, humedad, análisis de gas, posición, velocidad, fuerza, viscosidad, densidad, dureza, radioactividad, iluminación, contenido de polvo, concentración, presencia y cantidad de impurezas, tribodiagnósticos, acidez, contaminación, mediciones acústicas, mediciones eléctricas y otras mediciones.
El capítulo [15] del manual educativo “DISEÑO DE SISTEMAS DE CONTROL PARA LA PRODUCCIÓN AUTOMATIZADA FLEXIBLE” de la Universidad Politécnica de Tomsk está dedicado a la tarea de los sistemas de control automatizados en el diagnóstico operativo del estado de los equipos tecnológicos utilizando gráficos de control de Shewhart.
Conclusión
No ignore la naturaleza de la variabilidad. Integrar métodos inteligentes de control estadístico de procesos (Statistical Process Control, SPC) en sistemas automatizados de control de procesos y sistemas de control automatizados.